When you’re investing in a tube laser cutting machine, you’ll need to evaluate key specifications that directly impact your production capabilities. From power output ranging 1-6kW to material thickness capacity of 0.5-32mm, these parameters determine your operational efficiency. Your choice will affect throughput rates, precision levels, and ultimately your bottom line. Understanding the technical requirements and matching them to your specific business needs forms the foundation for a strategic equipment investment.
Key Takeaways
Assess your power requirements based on material types and thicknesses, choosing between 1kW to 6kW for optimal cutting performance.
Match cutting capabilities to your production needs, considering maximum dimensions and material compatibility with steel, aluminum, and specialized metals.
Ensure software compatibility with CAD/CAM systems and verify the control panel features support your workflow requirements.
Calculate space requirements, including loading zones, operational areas, and storage space, ensuring facility layout accommodates the entire workflow.
Consider automation features and maintenance costs, including consumables, energy consumption, and service contracts for long-term operational efficiency.
Understanding Core Technical Specifications and Power Requirements
Three critical technical specifications define a tube laser cutting machine’s capabilities: power output, cutting capacity, and positioning accuracy. You’ll need to determine the ideal power output, typically ranging from 1kW to 6kW, based on your material thickness and production requirements. Higher power doesn’t always translate to better performance – it’s about finding the right balance for your specific needs.
Consider your machine’s power consumption and overall machine efficiency when evaluating options. Modern tube lasers operate at 30-40% efficiency, converting electrical power into laser output. You’ll want to analyze the maximum tube dimensions the machine can handle and verify the positioning accuracy, which should be within ±0.02mm for precise cuts. These specifications directly impact your operational costs and production quality.
Material Types and Cutting Capabilities
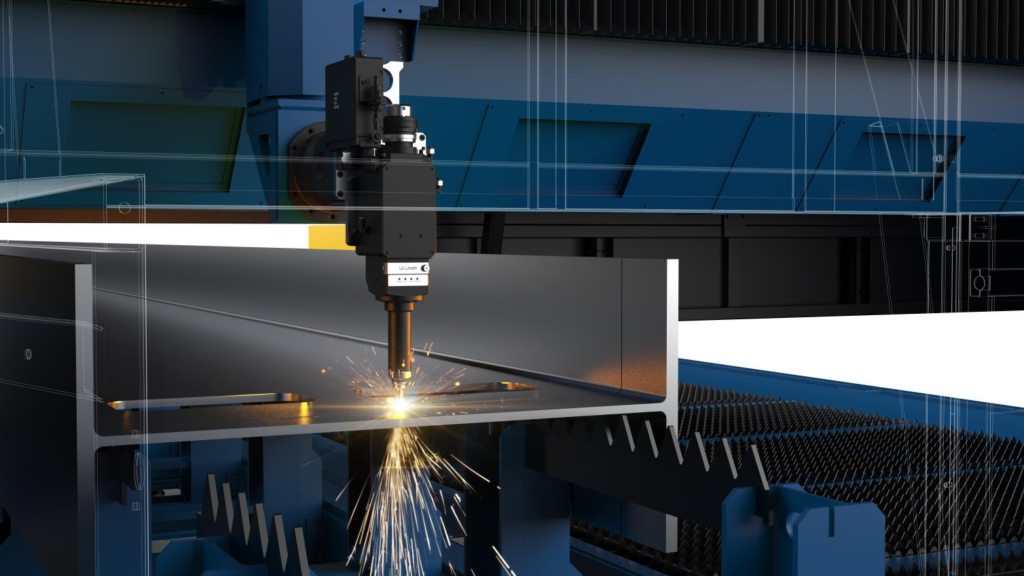
Building on the power specifications, your tube laser cutting machine‘s effectiveness depends heavily on its material compatibility and cutting capabilities. You’ll need to match your machine’s specifications to the materials you commonly process, considering both material composition and cutting thickness requirements.
Most modern tube lasers can handle mild steel up to 8mm, stainless steel up to 4mm, and aluminum up to 3mm. When evaluating machines, focus on their ability to cut your specific materials – whether that’s carbon steel, copper alloys, or specialized metals. The cutting thickness capacity directly impacts production speed and quality. For ideal results, ascertain your chosen machine offers the right combination of power output and cutting parameters for your material range, while maintaining tight tolerances and clean edge quality.
Software Integration and Control Systems
You’ll need to verify your tube laser cutting machine’s compatibility with industry-standard CAD/CAM software packages to guarantee seamless design-to-production workflows. The control panel should feature an intuitive interface with real-time monitoring capabilities, automated nesting functions, and precise parameter adjustment options. Modern systems often include remote operation features that let you manage multiple machines, monitor production status, and adjust cutting parameters from your smartphone or desktop computer.
CAD/CAM Software Compatibility
When selecting a tube laser cutting machine, compatibility with industry-standard CAD/CAM software platforms becomes a crucial technical consideration. You’ll need to verify your machine supports common file formats like DXF, IGES, and STEP, enabling seamless CAD compatibility across your design workflow. Modern tube laser systems should integrate with leading software solutions such as SolidWorks, AutoCAD, and specialized tube-cutting programs.
Your machine’s controller must facilitate smooth software integration with your existing production management systems. Look for features like network connectivity, real-time data exchange capabilities, and automated nesting functions. Consider whether the system offers built-in simulation tools, which can help you validate cutting paths and identify potential issues before actual production begins. The software should also provide advanced reporting features for quality control and production monitoring.
Control Panel Features
Three essential control panel features define a high-performance tube laser cutting system: an intuitive touchscreen interface, real-time monitoring capabilities, and customizable parameter controls.
You’ll need a user-friendly interface that displays critical data like cutting speed, power levels, and assist gas pressure in real-time. Look for systems offering multi-language support and gesture-based controls that streamline your operation workflow. The control panel should provide customizable settings for different materials and cutting scenarios, allowing you to save and recall specific parameters.
Advanced monitoring features should include automatic error detection, predictive maintenance alerts, and process optimization tools. Your control system must integrate seamlessly with your existing production software while offering remote access capabilities for monitoring operations from mobile devices or off-site locations.
Remote Operation Capabilities
Modern tube laser cutting machines leverage advanced software integration to enable extensive remote operations, from real-time monitoring to full system control. You’ll gain access to intuitive user interfaces that let you manage production schedules, adjust cutting parameters, and track machine performance from any connected device.
The remote monitoring capabilities allow you to receive instant notifications about machine status, maintenance requirements, and production metrics. You can analyze real-time data streams, optimize cutting processes, and troubleshoot issues without being physically present at the machine. Through secure network connections, you’re able to start, pause, or modify cutting operations, upload new design files, and coordinate multiple machines simultaneously. These remote features greatly reduce downtime, increase operational efficiency, and enable flexible production management across different work shifts or locations.
Automation Features and Production Efficiency
To maximize your production efficiency, you’ll want to evaluate tube laser cutting machines with automated loading systems that can handle your specific material dimensions and weights. Smart production management features like real-time monitoring, predictive maintenance alerts, and automated part sorting will help you reduce downtime and optimize workflow. Advanced automation capabilities can increase your machine utilization rate by up to 85%, greatly boosting your overall production capacity.
Automated Loading Systems
While manual loading processes can limit production rates to 30-40 tubes per hour, automated loading systems can boost throughput to 150-200 tubes per hour. You’ll find significant automated loading advantages in reduced labor costs, consistent material handling, and minimized operator fatigue.
Loading System Types | Max Tube Length | Throughput Rate |
---|---|---|
Bundle Loader | 24 ft | 200/hour |
Chain Conveyor | 40 ft | 175/hour |
Magnetic Lift | 32 ft | 150/hour |
When selecting your loading system, consider your production volume and tube specifications. Bundle loaders work best for high-volume operations with standardized materials, while chain conveyors offer flexibility for varying tube sizes. Magnetic lift systems provide gentle handling for delicate or finished materials. You’ll need to match your loading system’s capabilities with your production requirements to maximize efficiency.
Smart Production Management
Smart production management systems transform tube laser cutting efficiency by integrating real-time monitoring, automated workflow scheduling, and predictive maintenance protocols. You’ll gain extensive control over your production workflows through intelligent software that optimizes resource allocation and minimizes downtime.
These systems allow you to track material usage, monitor machine performance metrics, and adjust cutting parameters in real-time. You can analyze production data to identify bottlenecks and streamline operations while the software automatically schedules jobs based on priority, material availability, and machine capacity. The integrated maintenance alerts help you prevent costly breakdowns by signaling when components need attention before they fail. You’ll also benefit from detailed reporting features that provide insights into operational efficiency, helping you make data-driven decisions to improve productivity and reduce waste.
Maximizing Machine Uptime
Since production efficiency directly impacts your bottom line, maximizing tube laser cutting machine uptime requires implementing key automation features and operational protocols. You’ll need to establish a robust preventive maintenance schedule that includes regular system diagnostics, cutting head inspections, and beam alignment checks.
Integrate automated material handling systems and nesting software to reduce setup times and material waste. Implement real-time monitoring systems to track machine performance metrics and conduct regular downtime analysis. This data helps identify bottlenecks and recurring issues before they cause significant disruptions.
You can further boost uptime by utilizing automatic nozzle cleaning, height sensing, and breakthrough detection features. Install automated parts sorting and collection systems to maintain continuous operation while minimizing operator intervention. These automation solutions typically increase productivity by 30-40% compared to manual operations.
Maintenance Considerations and Operating Costs
Because tube laser cutting machines represent a significant capital investment, understanding their maintenance requirements and operating costs is essential for accurate budgeting. Regular maintenance routines protect your investment while minimizing downtime and unexpected repairs. You’ll need to perform a detailed cost analysis that includes both direct and indirect operational expenses.
- Monthly consumables costs, including assist gases, nozzles, and lens replacements, typically range from 5-15% of your operating budget
- Preventive maintenance schedules should allocate 8-10 hours per month for inspections, cleaning, and calibration
- Energy consumption varies by laser power, averaging 25-40 kW/hour during operation
- Replacement parts and service contracts can cost 3-7% of the machine’s purchase price annually
Plan for these ongoing expenses while implementing a proactive maintenance strategy to maximize your machine’s lifespan and performance.
Space Requirements and Facility Integration
Planning out your facility layout must account for more than just the machine’s footprint. You’ll need to take into account material loading zones, finished product storage, and maintenance access areas for ideal space utilization. Most tube laser systems require dedicated utilities, including power supply, ventilation, and compressed air.
Area Type | Minimum Space (ft²) | Purpose |
---|---|---|
Loading Zone | 200 | Material staging |
Machine Area | 400 | Cutting operations |
Storage Zone | 300 | Finished products |
Layout enhancement should incorporate workflow analysis to minimize material handling distances. Guarantee adequate ceiling height (typically 12-15 feet) for loading operations and factor in safety zones around the machine. You’ll also need to plan for auxiliary equipment placement, such as dust collection systems and cooling units, which can impact your overall space requirements.
Conclusion
Your success in tube laser cutting hinges on selecting equipment that matches your technical requirements, accommodates your material needs, and aligns with your production goals. By evaluating power specifications, automation features, and software compatibility, you’ll optimize operational efficiency and ROI. Consider both immediate cutting demands and future scalability to guarantee your investment delivers consistent performance and maintains competitive advantage in precision manufacturing.