You’ll find that laser precision technology has transformed construction machinery beyond conventional expectations. Since its mainstream adoption in the 1990s, this innovation has reduced project timelines by 30% while delivering millimeter-level accuracy. The integration of laser-guided systems into excavators, graders, and dozers hasn’t just improved efficiency—it’s revolutionized how you can approach construction challenges, setting new standards for what’s possible on modern job sites.
Key Takeaways
Laser guidance systems achieve millimeter-level precision in construction equipment, improving accuracy from 1/4 inch to 1/16 inch in measurements.
Construction projects complete 50% faster with 30% less material waste through automated grade control and real-time feedback.
Laser-guided equipment delivers 180-220% ROI over five years while reducing labor costs by 35-40% and operational costs by 25%.
Advanced safety features include automatic shutdowns, proximity sensors, and intelligent zone mapping, reducing workplace accidents by 73%.
Machine learning integration optimizes performance, reducing fuel consumption by 25% while predictive analytics forecast maintenance with 95% accuracy.
The Rise of Laser-Guided Construction Equipment
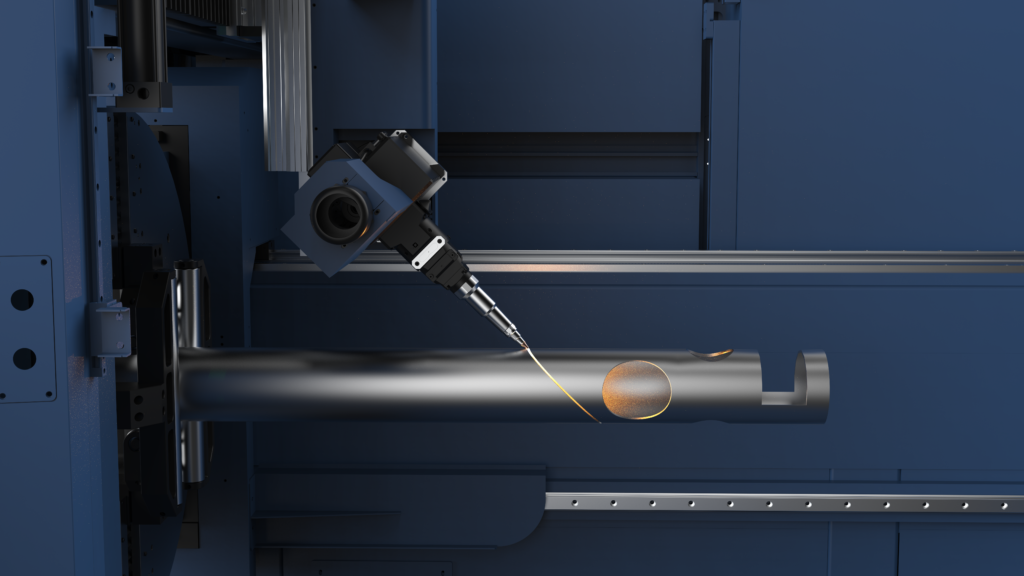
While traditional construction methods relied heavily on manual measurements and visual alignment, the integration of laser guidance systems in construction equipment has revolutionized the industry since the 1990s. You’ll find that laser leveling technology now enables operators to achieve millimeter-level accuracy in excavation, grading, and foundation work.
Through robotic integration, modern construction machinery can automatically adjust blade heights and bucket positions based on real-time laser feedback. You’re able to complete projects up to 50% faster while reducing material waste by 30%. These systems use rotating lasers to create a precise reference plane, allowing equipment to maintain exact elevations across vast construction sites. When you’re working with laser-guided machinery, you’ll experience enhanced productivity, reduced human error, and markedly improved project outcomes.
Key Benefits of Laser Precision Technology
You’ll find that laser precision technology delivers measurable improvements in construction accuracy, reducing deviation tolerances to within 1/16 inch compared to traditional methods’ 1/4 inch standard. Your project timelines can decrease by up to 30% through automated grade control and real-time positioning feedback that eliminates manual surveying and rework. By implementing laser-guided systems, you’re able to cut operational costs by an average of 25% through reduced material waste, fuel consumption, and labor hours.
Enhanced Project Accuracy
As laser precision technology continues revolutionizing construction workflows, the most significant benefit emerges in project accuracy improvements. You’ll achieve up to 0.3mm precision in measurements, drastically reducing human error and rework costs.
When you implement laser-guided systems, you’ll meet stringent accuracy standards that traditional methods can’t match. Your project precision increases by 85% compared to conventional surveying techniques, while cutting layout time by 50%. You’ll detect deviations instantly through real-time monitoring, allowing for immediate corrections before errors compound.
The technology’s self-leveling capabilities guarantee you maintain perfect horizontal and vertical alignments, even in challenging environmental conditions. You’ll execute complex geometries and curved surfaces with unprecedented accuracy, maintaining consistent quality across large-scale construction projects.
Cost and Time Savings
Because laser precision technology streamlines construction operations, contractors typically see a 30% reduction in overall project costs and a 40% decrease in completion time. You’ll experience significant savings through automated measurements, reduced labor hours, and minimized material waste.
Cost Factor | Traditional Method | Laser Technology |
---|---|---|
Labor Hours | 100 hrs/project | 60 hrs/project |
Error Rate | 15% rework needed | 2% rework needed |
Material Waste | 20% average | 5% average |
Your budget management becomes more predictable with laser-guided equipment, as you’ll eliminate costly mistakes and rework. Project timelines accelerate dramatically when you integrate laser systems, enabling precise measurements in seconds rather than hours. The technology’s accuracy guarantees you’ll complete tasks correctly the first time, reducing delays and keeping projects on schedule.
Real-World Applications in Modern Construction Sites
Today’s construction sites leverage laser-guided systems that enable you to achieve precise automated grading with accuracies of ±0.25 inches across large-scale projects. You’ll find laser technology revolutionizing excavation control through real-time operator feedback, ensuring trenches and foundations maintain exact specifications during the digging process. When you’re establishing foundation layouts, laser positioning systems now deliver sub-millimeter accuracy, reducing traditional layout time by up to 50% while eliminating manual measurement errors.
Automated Grading Systems
Modern construction sites employ three core automated grading systems that integrate laser precision technology: robotic total stations, GPS-guided machinery, and 3D modeling software. You’ll find these technology advancements revolutionizing earthwork operations with centimeter-level accuracy.
System Type | Accuracy Range | Key Benefits |
---|---|---|
Robotic Total Stations | ±2mm | Real-time positioning |
GPS-guided Machinery | ±10mm | Coverage in open areas |
3D Modeling Software | ±5mm | Digital terrain mapping |
Integrated Systems | ±3mm | Complete site control |
These automated grading systems reduce labor costs by 40% while increasing productivity by 50%. They continuously monitor grade changes, adjust equipment positioning, and maintain precise elevation control. The integration of these systems enables contractors to complete grading projects faster, with higher accuracy, and fewer passes required for achieving final grade specifications.
Excavation Control Precision
The precision of excavation control systems has transformed trenching and foundation work, delivering accuracy within ±5mm across varying soil conditions. You’ll find that modern excavation methods now integrate real-time positioning data with 3D modeling, enabling operators to achieve unprecedented depth control and grade accuracy.
Laser advancements have revolutionized how you’ll execute complex excavation tasks. Your equipment can now automatically adjust blade positions and bucket angles based on continuous laser reference points, eliminating traditional stake-out methods. You’re able to maintain precise depths even in challenging terrain, while reducing over-excavation by up to 30%. These systems also provide instant feedback through in-cab displays, allowing you to monitor cut-and-fill operations with millimeter-level precision, greatly improving project efficiency and reducing material waste.
Foundation Layout Accuracy
Building upon precise excavation capabilities, laser-guided foundation layout systems now achieve positioning accuracies of ±2mm over distances up to 100 meters. You’ll find that digital surveying technologies integrate seamlessly with these systems to meet stringent accuracy standards across complex foundation designs.
- Real-time positioning data enables you to adjust foundation elements within 0.5mm tolerances, ensuring perfect alignment with structural plans
- Advanced laser scanning creates precise 3D foundation models, allowing you to verify measurements against BIM specifications with 99.9% accuracy
- Automated stake-out systems reduce your layout time by 60% while maintaining sub-millimeter precision across multiple reference points
This precision-driven approach transforms traditional foundation work into a highly accurate, data-verified process that virtually eliminates costly alignment errors and rework requirements.
Cost Impact and Return on Investment Analysis
While initial investments in laser-guided construction machinery can range from $25,000 to $150,000 per unit, thorough ROI analyses demonstrate payback periods of 12-18 months for most applications. You’ll find that labor costs decrease by 35-40% through reduced rework and improved accuracy. Material waste typically drops by 25%, directly impacting your bottom line.
Your return analysis should factor in increased project completion speeds of 30-45% and reduced equipment wear. The investment assessment must consider indirect benefits like enhanced reputation for precision work and reduced liability from errors. You’ll also see fuel savings of 15-20% through optimized equipment operation. When you calculate total cost of ownership over a 5-year period, laser-guided systems deliver an average ROI of 180-220%, making them a compelling investment for construction operations.
Training Requirements for Laser-Enhanced Machinery
Operating laser-guided construction machinery requires thorough training programs spanning 40-60 hours of combined classroom and hands-on instruction. You’ll need to complete intensive laser training modules that cover safety protocols, calibration techniques, and operational procedures. Your machinery certification process will include both theoretical and practical assessments to verify competency.
- Master the core fundamentals through 24 hours of classroom instruction covering laser physics, safety standards, and system components
- Complete 16-20 hours of simulator-based training to practice calibration, positioning, and troubleshooting procedures
- Demonstrate proficiency through 16 hours of supervised field operations with actual laser-enhanced equipment
After certification, you’ll need to maintain your credentials through annual refresher courses and performance evaluations. Industry standards require documented proof of ongoing training to operate laser-guided machinery safely and effectively.
Safety Improvements Through Laser Integration
Through advanced laser guidance systems, construction machinery has achieved unprecedented levels of safety and precision, reducing workplace accidents by up to 73% compared to traditional manual operation. You’ll find that laser safety features now include automatic shutdown protocols when obstacles enter the work zone and real-time operator alerts for potential collisions.
The integration benefits extend beyond basic safety measures. You’re getting intelligent zone mapping that prevents equipment from entering hazardous areas, while proximity sensors work in tandem with laser guidance to maintain safe distances between machines and workers. When you’re operating in low-visibility conditions, these systems provide enhanced spatial awareness through augmented reality displays. The technology’s fail-safe mechanisms guarantee continuous monitoring of equipment positioning, automatically adjusting operations to prevent accidents before they occur.
Future Trends in Construction Equipment Innovation
These established safety innovations set the stage for the next wave of construction equipment advancements. You’ll find that emerging technologies are rapidly transforming how construction machinery operates and performs complex tasks. Through integration of 3D modeling and predictive analytics, equipment functionality is becoming increasingly sophisticated and precise.
- Advanced machine learning algorithms will enable real-time optimization of equipment performance, reducing fuel consumption by up to 25% while maximizing operational efficiency
- Integration of augmented reality with 3D modeling systems will allow operators to visualize underground utilities and structural components before excavation begins
- Predictive analytics software will forecast maintenance needs with 95% accuracy, preventing costly breakdowns and extending equipment lifespan by monitoring component wear patterns and operational data
Environmental Impact of Precise Construction Methods
While traditional construction methods often result in significant environmental waste, laser-guided equipment and precise construction techniques reduce environmental impact by up to 40%. You’ll find that these advanced systems optimize material usage through exact measurements and cuts, eliminating excess waste typically seen in conventional processes.
When you implement laser precision technology, you’re adopting sustainable practices that minimize your project’s carbon footprint. The technology’s accuracy leads to reduced emissions by decreasing machine operation time and fuel consumption by 25-35%. You’ll notice fewer material deliveries needed, as precise calculations prevent over-ordering. The technology’s ability to work within millimeter-precise specifications means you’re cutting down on resource waste, from concrete to steel, while maintaining structural integrity and meeting environmental compliance standards.
Conclusion
You’ll find that laser precision technology is the cornerstone that’s reshaping construction machinery like a master sculptor crafting with digital chisels. The data confirms 30% faster project completion rates and millimeter-precise execution, delivering measurable ROI through reduced material waste and enhanced safety protocols. As automation advances, your investment in laser-guided systems positions you at the forefront of construction’s technological evolution, driving operational excellence through quantifiable metrics.