You’ll find that modern welding technologies have evolved far beyond the simple fusion of metals through heat and pressure. While laser welding can achieve penetration depths of up to 25mm in a single pass, TIG welding typically maxes out at 6mm without multiple passes. This stark difference in capability represents just one aspect of the complex trade-offs between these two distinct welding methods. Understanding their unique characteristics will help you make vital decisions for your manufacturing processes.
Key Takeaways
?Laser welding operates 10-20 times faster than TIG welding, reaching speeds of 150-200 inches per minute versus 4-20 inches per minute.
?TIG welding provides superior control and versatility across materials, while laser welding excels in automated, high-precision applications.
?Laser welding creates deeper, narrower welds with minimal heat-affected zones, while TIG produces wider, more aesthetically pleasing welds.
?TIG welding requires simpler equipment setup and lower initial costs, while laser welding demands specialized power sources and cooling units.
?Laser welding works best on thin materials (0.1-6mm), while TIG handles thicker materials (0.5-8mm) and is better for reflective metals.
Key Principles and Basic Operation
While both laser and TIG welding create precision joints through localized heating, their fundamental operating principles differ markedly. In laser welding, you’ll direct a concentrated beam of photons onto the workpiece, creating intense, focused heat that rapidly melts the material. The process requires minimal contact and generates a narrow heat-affected zone, making it ideal for precise, automated applications.
TIG welding, conversely, relies on an electric arc established between a non-consumable tungsten electrode and your workpiece. You’ll need to maintain a careful balance of current, arc length, and filler metal addition while protecting the weld pool with inert gas. These welding techniques each offer distinct process advantages: laser welding excels in speed and automation potential, while TIG provides superior control and versatility across material types. You’ll find laser welding particularly effective for thin materials and high-volume production, whereas TIG welding proves invaluable for detailed, manual welding tasks requiring exceptional finish quality.
Equipment Requirements and Setup
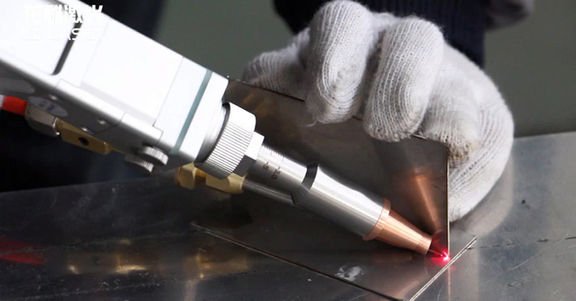
You’ll need distinctly different equipment setups for laser and TIG welding, with laser systems requiring specialized power sources, cooling units, and beam delivery components while TIG setups need gas cylinders, torch assemblies, and foot pedals. For laser welding, you’ll need a dedicated facility with proper ventilation and safety features, plus 220V or higher power supply, whereas TIG welding can often operate on standard 110V circuits in smaller spaces. Both processes require proper safety equipment, including specialized eye protection – laser-specific safety goggles for laser welding and standard welding helmets for TIG.
Basic Tools and Accessories
Both laser and TIG welding require distinct sets of essential tools and equipment for safe, successful operation. For laser welding, you’ll need protective eyewear specifically rated for laser wavelengths, beam delivery systems, cooling units, and automated positioning equipment. Modern welding techniques have introduced advanced laser power sources with precise control interfaces.
With TIG welding, you’ll require tungsten electrodes, collets, gas lenses, ceramic nozzles, and foot pedals for amperage control. Tool innovations have improved TIG torch ergonomics and heat management capabilities. Both processes demand proper filler materials, work clamps, and material cleaning supplies. You’ll also need process-specific safety gear: heat-resistant gloves, face shields, and flame-resistant clothing. For best results, maintain a complete set of measurement tools, including calipers and thickness gauges, regardless of which method you choose.
Power and Space Needs
Although laser and TIG welding systems serve similar purposes, their power and space requirements differ remarkably. TIG welding typically requires a 220V power supply for industrial applications, though you’ll find some units operating on 110V for lighter work. The power consumption ranges from 3-10 kW, depending on material thickness and welding speed.
Laser welding systems demand considerably higher power inputs, often consuming 15-50 kW, but they’re more energy-efficient during operation. You’ll need to weigh spatial constraints carefully – TIG welding setups require modest floor space for the power source, cooling unit, and operator workspace. In contrast, laser welding systems need additional room for safety enclosures, beam delivery systems, and cooling infrastructure. You’ll also need dedicated ventilation systems and possibly specialized electrical installations for both methods, though laser systems have more stringent requirements.
Weld Quality and Penetration Characteristics
The distinct penetration profiles of laser and TIG welding create markedly different quality outcomes in finished welds. You’ll find that laser welding produces narrow, deep penetration with minimal heat-affected zones, while TIG creates wider, shallower welds with superior weld aesthetics. Laser’s concentrated energy achieves penetration depths up to 10 times greater than TIG in a single pass.
Characteristic | Laser Welding | TIG Welding |
---|---|---|
Penetration | Deep, narrow | Shallow, wide |
Heat Zone | Minimal | Extensive |
Surface Finish | Good | Excellent |
When examining weld quality, you’ll notice that TIG excels in controlling the weld pool, producing smooth, visually appealing welds ideal for visible applications. Laser welding’s precision makes it superior for automated processes and thin materials, though it can create undercuts if parameters aren’t precisely controlled. Your choice between these methods should depend on your specific requirements for penetration depth and surface finish quality.
Speed and Productivity Comparison
Welding speed represents a major differentiator between laser and TIG processes, directly impacting overall production efficiency. You’ll find that laser welding operates at considerably higher speeds, typically 10-20 times faster than TIG welding in comparable applications. This dramatic difference in welding speed translates to substantial productivity enhancement in manufacturing settings.
When you’re using TIG welding, you’ll achieve speeds of roughly 4-20 inches per minute, depending on material thickness and joint configuration. In contrast, laser welding can reach speeds of 150-200 inches per minute under ideal conditions. This increased speed stems from laser welding’s concentrated heat input and minimal heat-affected zone.
You can further maximize productivity with laser welding through automation integration and multi-head systems, enabling simultaneous welds. While TIG welding requires manual electrode manipulation and filler material addition, laser systems can be programmed for continuous operation, reducing downtime and operator fatigue.
Material Compatibility and Limitations
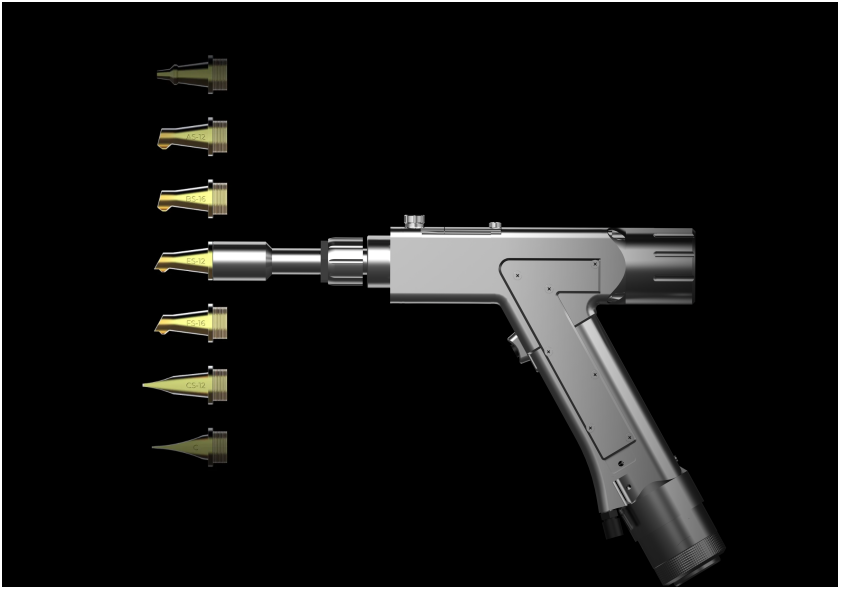
Both laser and TIG welding demonstrate distinct capabilities when processing different materials, with each method exhibiting specific strengths and limitations. You’ll find that TIG welding excels with aluminum, copper, magnesium, and stainless steel, offering superior material suitability for these metals due to its precise heat control and strong weld integrity.
Laser welding, while more restricted in material compatibility, provides exceptional results with steel, titanium, and nickel alloys. You won’t be able to weld highly reflective materials easily with lasers, as they can scatter the beam and reduce efficiency. However, laser welding‘s concentrated heat input allows you to join dissimilar metals that TIG welding can’t handle effectively.
When evaluating thickness limitations, TIG welding handles materials from 0.5mm to 8mm efficiently, while laser welding performs best on thinner materials, typically 0.1mm to 6mm, though specialized systems can process thicker sections.
Cost Analysis and Investment Considerations
Understanding material capabilities directly impacts your financial planning when choosing between laser and TIG welding systems. You’ll need to take into account both initial equipment costs and long-term operational expenses. Laser welding systems typically require a $150,000-$500,000 investment, while TIG setups range from $2,000-$15,000.
Your cost breakdown should factor in power consumption, maintenance requirements, and consumables. Laser systems consume more electricity but require fewer consumables, while TIG welding demands regular electrode and shielding gas replacement. Labor costs vary considerably – laser welding offers faster processing speeds and automation potential, reducing labor hours by up to 75% compared to TIG.
Calculate your investment return by analyzing production volume, material thickness, and application complexity. If you’re handling high-volume precision work, laser welding’s speed and automation capabilities often justify its higher initial cost. For lower-volume or varied applications, TIG welding’s flexibility and lower startup costs might prove more economical.
Applications Across Industries
Three major industrial sectors showcase distinct advantages of laser and TIG welding technologies. In automotive manufacturing, you’ll find laser welding dominating high-speed production lines for body panels and precision components, while TIG welding excels in custom exhaust system fabrication. The medical devices sector relies on laser welding’s ultra-precise capabilities for surgical instruments and implants, whereas TIG welding supports larger medical equipment assembly.
Aerospace components demand both methods: laser welding for intricate turbine parts and electronic assemblies, with TIG welding handling structural joints and repairs. You’ll discover precision engineering applications across jewelry design, where laser welding creates microscopic joints, and TIG welding forms artistic sculptures. In construction materials, TIG welding remains the go-to choice for structural steel, while laser welding revolutionizes the joining of advanced composites and specialized alloys, offering unmatched versatility in modern industrial applications.
Safety Measures and Operator Training
When you’re working with laser or TIG welding equipment, you’ll need specialized protective gear including auto-darkening helmets, fire-resistant clothing, and appropriate eye protection designed for specific wavelengths and power levels. You’ll find that certification requirements differ between these processes, with laser welding typically demanding additional training in radiation safety and automated systems operation. Risk prevention protocols must be strictly followed, including proper ventilation systems, emergency shutdown procedures, and regular equipment maintenance checks to guarantee both laser and TIG welding operations remain safe.
Protective Equipment and Gear
Both laser and TIG welding require extensive personal protective equipment (PPE) to shield operators from hazardous radiation, fumes, and intense light. When performing laser welding, you’ll need specialized laser safety goggles rated for your specific wavelength, while TIG welding requires auto-darkening helmets with appropriate shade ratings. Your protective gear must include flame-resistant clothing, leather gloves, and steel-toed boots for both processes.
For laser welding, you’ll need additional protection like beam enclosures and remote monitoring systems to meet safety standards. TIG welding requires heat-resistant arm sleeves and a respirator for fume protection. Both processes demand proper ventilation systems to extract harmful gases and particulates. Remember to inspect all PPE before each use and replace damaged items immediately to maintain superior protection.
Certification Requirements
Due to their inherent safety risks, laser and TIG welding operations require specific certifications and extensive training programs. You’ll need to complete certification pathways that include both theoretical knowledge and hands-on skill assessment testing. For laser welding, you must obtain laser safety officer (LSO) certification, while TIG welding requires AWS certification.
Requirement | Laser Welding | TIG Welding |
---|---|---|
Basic Cert | LSO Training | AWS D1.1 |
Experience | 40 Hours | 1000 Hours |
Renewal | Every 2 Years | Every 3 Years |
Before operating either system, you’ll need documented proof of completing OSHA safety courses and equipment-specific training. Many employers also require additional in-house certifications focusing on your facility’s specific procedures and quality control standards.
Risk Prevention Protocols
Proper certification forms the foundation for implementing extensive risk prevention protocols in both laser and TIG welding operations. Before beginning any welding task, you’ll need to conduct a thorough risk assessment of your workspace, identifying potential hazards unique to each welding method. For laser welding, you must install beam containment systems and maintain strict access controls to prevent accidental exposure. With TIG welding, you’ll focus on electrical safety and proper ventilation systems.
You’ll need to establish clear emergency protocols for both processes, including equipment shutdown procedures and first aid responses. Verify you’ve installed appropriate fire suppression systems, maintain properly calibrated monitoring devices, and keep personal protective equipment readily available. Regular safety drills and equipment inspections are essential components of your risk prevention strategy.
Maintenance and Troubleshooting
While laser and TIG welding systems offer distinct advantages, they each require specific maintenance protocols and troubleshooting approaches to maintain peak performance. You’ll need to conduct routine inspections of both systems, but with different focus areas. For laser welding, check the optical components and beam delivery system, while TIG welding requires electrode inspection and gas flow verification.
When implementing troubleshooting techniques, consider these critical aspects:
- Power source diagnostics – Test input voltage, verify connections, and monitor output consistency for both systems
- Consumable components – Check laser mirrors and lenses for damage or contamination; inspect TIG tungsten electrodes for wear and proper grinding angles
- Shielding gas delivery – Monitor gas flow rates, verify line integrity, and test for leaks in both systems
Remember to document all maintenance activities and calibrate equipment regularly to guarantee consistent weld quality and minimize downtime during production.
Conclusion
When you’re weighing laser welding against TIG welding, it’s not a clear-cut decision. While laser welding hits the nail on the head for high-speed precision and minimal heat distortion, TIG welding offers superior control and versatility across material types. You’ll need to analyze your specific requirements, including production volume, material thickness, and investment capacity, to determine which technology aligns with your manufacturing objectives.