When you’re exploring the intricate world of laser pipe cutting, you’ll discover a convergence of engineering precision and artistic possibility. Modern fiber laser systems can transform raw metal tubes into sophisticated components with tolerances tighter than a human hair. The mastery of this technology involves understanding both the technical parameters and creative potential, from optimizing cutting sequences to developing complex patterns that push the boundaries of traditional fabrication.
Key Takeaways
Modern pipe laser cutting systems achieve micron-level precision through advanced CNC motion control and real-time monitoring systems.
CAD/CAM software enables creation of intricate patterns and complex geometric designs with consistently tight tolerances across multiple pipe sections.
Fiber laser technology delivers superior edge quality and faster cutting speeds compared to traditional methods, reducing production time by 60%.
Material selection and properties directly influence cutting parameters, requiring precise matching of laser type to achieve optimal results.
Integration of AI and IoT sensors allows automatic adjustment of cutting parameters, ensuring artistic precision while maintaining production efficiency.
The Evolution of Pipe Laser Cutting Technology
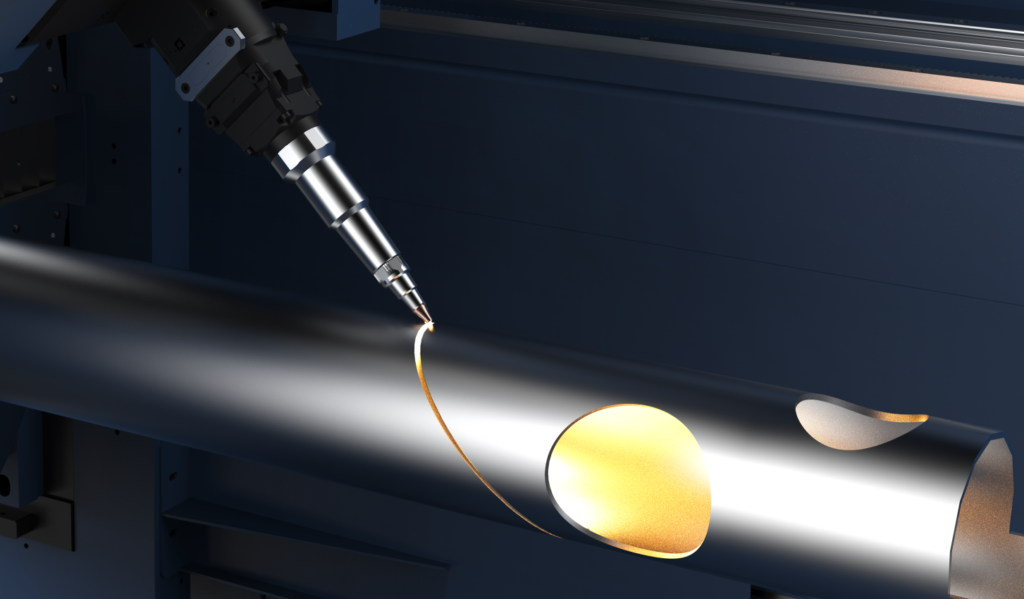
As industrial manufacturing entered the digital age, pipe laser cutting technology transformed from basic automated torch systems into sophisticated computer-controlled machines. You’ll find that technological advancements in beam focusing, power delivery, and motion control have revolutionized the precision capabilities of these systems.
Through industry adoption of fiber laser technology, you’re now able to achieve faster cutting speeds and superior edge quality compared to traditional CO2 lasers. Today’s systems incorporate advanced features like 3D rotating heads, real-time monitoring, and adaptive optics that automatically adjust to varying pipe diameters. You can program complex cutting patterns with CAD/CAM integration, while smart sensors guarantee prime beam positioning and material handling. These innovations have considerably reduced setup times and material waste, making pipe laser cutting more efficient and cost-effective than ever before.
Understanding Core Components of Laser Cutting Systems
Modern laser cutting systems consist of five essential components that work in harmony to achieve precise pipe cutting operations. You’ll find the laser resonator, which generates the high-powered beam, working alongside the beam delivery system that guides the laser to its target. The cutting head focuses the beam and delivers assist gas, while the CNC motion system controls the movement with micron-level precision.
Understanding laser technology fundamentals is vital when working with the fifth component – the control system. This sophisticated interface manages beam parameters, motion coordination, and cutting sequences. Each of these laser cutting components must be properly calibrated and maintained to guarantee peak performance. When you’re operating these systems, remember that the synchronization between these core elements determines the quality of your final cuts.
Material Selection and Compatibility in Pipe Processing
When selecting materials for laser pipe cutting, you’ll need to evaluate multiple factors including thermal conductivity, surface reflectivity, and material thickness. Material properties directly impact your cutting parameters and overall fabrication efficiency. Common materials like carbon steel, stainless steel, and aluminum each require specific processing techniques due to their unique characteristics.
You’ll achieve ideal results by matching your laser type to the material’s compatibility requirements. CO2 lasers work well with non-reflective materials, while fiber lasers excel at cutting reflective metals. Consider your material’s melting point, thermal expansion coefficient, and oxidation resistance when setting up your cutting parameters. These factors influence cut quality, processing speed, and edge finish. Always verify your material’s composition and condition before beginning to uphold consistent results.
Advanced Design Capabilities and Pattern Creation
The precision control of laser pipe cutting systems enables intricate pattern creation and complex geometric designs that were previously impossible with traditional methods. You’ll find that advanced CAD/CAM software integration allows you to develop sophisticated patterns while maintaining tight tolerances and dimensional accuracy throughout the cutting process.
Through pattern innovation, you can create repeatable designs across multiple pipe sections, including spirals, meshes, and interconnected geometries. The design flexibility lets you adjust pattern density, spacing, and orientation in real-time. You’re able to prototype new designs quickly and modify existing patterns to meet specific structural or aesthetic requirements. By leveraging these capabilities, you can produce custom perforations, ventilation holes, and decorative elements while ensuring consistent quality across production runs.
Quality Control Measures in Laser-Cut Pipe Production
Maintaining strict quality control standards during laser pipe cutting operations requires implementing thorough inspection protocols and real-time monitoring systems. You’ll need to establish clear quality metrics and performance benchmarks to guarantee consistent output.
Your process standardization should include automated defect identification systems that scan for surface irregularities, dimensional accuracy, and material integrity. You can integrate real-time monitoring tools that track cutting parameters, beam alignment, and material flow throughout the production cycle.
To meet compliance regulations, you’ll want to implement extensive inspection techniques using both automated and manual methods. Set up feedback loops that connect quality data with process adjustments, allowing for immediate corrections when deviations occur. Remember to document all quality control measures and maintain detailed records of inspection results for traceability and continuous improvement purposes.
Cost-Efficiency and ROI in Modern Pipe Fabrication
Modern pipe fabrication facilities can maximize their return on investment through strategic implementation of automated laser cutting systems and optimized workflow processes. You’ll achieve significant cost benefits by integrating these advanced technologies into your production line, particularly when you consider the reduced material waste and labor requirements.
- Automated systems decrease operational costs by up to 30% while increasing production speed and accuracy
- Real-time monitoring and quality control features minimize rework and scrap material expenses
- Preventive maintenance scheduling optimizes machine uptime and extends equipment lifespan
To maximize your investment return, focus on thorough operator training and regular system updates. You’ll find that proper implementation of laser cutting technology transforms your production efficiency, leading to faster turnaround times and higher profit margins. Consider conducting quarterly performance analyses to track your facility’s productivity improvements and adjust processes accordingly.
Environmental Impact and Sustainable Practices
Sustainable pipe fabrication practices have become increasingly critical in today’s environmentally conscious manufacturing landscape. You’ll find that eco-friendly technologies in laser cutting substantially reduce waste and energy consumption compared to traditional methods. Through sustainable sourcing of raw materials and optimized production processes, you’re able to minimize your environmental footprint while maintaining high-quality output.
Practice | Environmental Benefit |
---|---|
Laser Precision | 90% Less Material Waste |
Energy Management | 40% Power Reduction |
Material Recycling | 85% Resource Recovery |
Water Conservation | 60% Usage Reduction |
Your implementation of closed-loop cooling systems and scrap metal recycling programs directly contributes to resource conservation. By adopting these practices, you’ll not only comply with environmental regulations but also position your operation as a leader in sustainable manufacturing, while potentially reducing operational costs through improved efficiency.
Safety Protocols and Operator Training
While operating precision pipe and laser cutting equipment demands rigorous attention to safety, you’ll need extensive protocols and training systems to protect workers and maintain operational efficiency. Before accessing any machinery, you must complete thorough operator certification programs and regular safety assessments.
Key safety requirements include:
- Wearing appropriate Personal Protective Equipment (PPE), including laser-safe eyewear and flame-resistant clothing
- Maintaining emergency shutdown procedures and ensuring proper ventilation systems are operational
- Conducting daily equipment inspections and calibration checks before starting operations
You’ll need to document all training sessions and maintain updated safety records. Regular performance evaluations help identify areas where additional training might be necessary, ensuring your facility maintains the highest safety standards while maximizing production efficiency.
Industry Applications and Case Studies
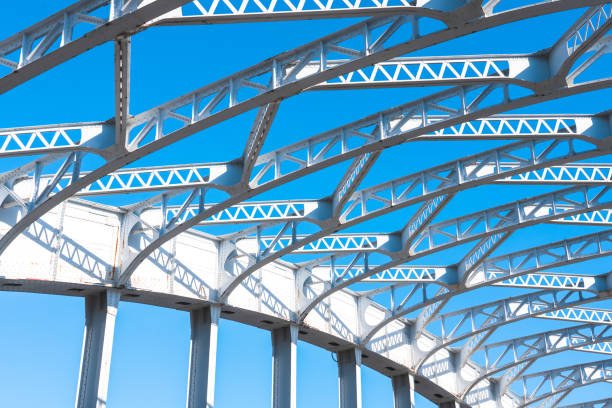
You’ll find precision pipe and laser cutting technologies revolutionizing aerospace manufacturing through complex tubular components used in hydraulic systems and structural frameworks. In medical equipment production, you’re seeing these techniques enable the creation of surgical instruments and implantable devices with tolerances as precise as 0.001 inches. The oil and gas sector demonstrates these capabilities through custom-fabricated pipeline components that withstand extreme pressures and corrosive environments while maintaining critical safety standards.
Aerospace Engineering Breakthroughs
Three major aerospace engineering breakthroughs have revolutionized precision pipe and laser cutting applications in modern aircraft manufacturing. You’ll find these advancements have transformed how precision engineering integrates with aerospace materials processing.
Advanced fiber laser systems now achieve cuts within 0.001mm tolerance on titanium alloy components, enabling perfect fits for critical engine assemblies and hydraulic systems
Multi-axis robotic laser cutting platforms can process complex curved geometries in aerospace-grade aluminum pipes, reducing manufacturing time by 60% while maintaining structural integrity
Real-time adaptive control systems automatically adjust cutting parameters based on material variations, ensuring consistent quality across different aerospace materials and thicknesses
These innovations have dramatically improved manufacturing efficiency while meeting the aerospace industry’s stringent safety and performance requirements.
Medical Equipment Manufacturing
Since medical equipment demands exceptional cleanliness and precision, laser cutting applications have become essential in manufacturing surgical instruments, implants, and diagnostic devices. You’ll find that laser cutting meets strict medical standards while ensuring consistent quality across production runs.
When you’re working with medical-grade materials, you’ll need to adhere to precision regulations that govern equipment manufacturing. Laser cutting systems offer the equipment adaptability you require, allowing you to switch between different material types and thicknesses without compromising accuracy. Through innovative technologies like fiber lasers and ultra-precise beam control, you can achieve intricate cuts for stents, surgical tools, and medical device components. The non-contact nature of laser cutting also eliminates material contamination, making it ideal for creating sterile medical equipment that meets industry requirements.
Oil Pipeline Solutions
While traditional pipe manufacturing methods remain common, laser cutting technology has revolutionized oil pipeline production by enabling precise, high-speed fabrication of critical components. You’ll find that modern pipeline design integrates advanced corrosion resistance features and energy efficiency measures through precise laser-cut joints and fittings.
- Technology integration allows real-time monitoring of pipeline integrity, enhancing risk management and regulatory compliance
- Project management benefits from streamlined logistics optimization, reducing installation time and material waste
- Laser-cut components guarantee exact specifications for critical connection points, improving long-term reliability
When you’re planning oil pipeline installations, laser cutting’s precision becomes essential for meeting stringent safety standards. The technology’s ability to create complex geometries supports innovative flow control solutions while maintaining structural integrity throughout the system’s lifecycle.
Maintenance and System Optimization
Regular maintenance and system enhancement are crucial components for maximizing the performance of precision pipe and laser cutting equipment. You’ll need to implement preventive maintenance schedules and conduct system diagnostics regularly to guarantee peak operation. Monitor your equipment’s essential parameters and address issues before they escalate into costly repairs.
Component | Enhancement Action |
---|---|
Laser Head | Clean optics weekly |
Gas System | Check pressure daily |
Motion Control | Calibrate monthly |
Cooling System | Test fluid quality |
Software | Update parameters |
Keep detailed maintenance logs and analyze performance trends to identify potential improvements. You’ll want to adjust cutting parameters based on material types and thicknesses, guaranteeing consistent quality while maximizing throughput. Remember to inspect assist gas systems and verify beam alignment to maintain precise cuts and extend equipment life.
Future Trends in Pipe Laser Cutting
As technological advancements accelerate, pipe laser cutting is evolving toward more automated, intelligent systems that incorporate AI-driven process enhancement and predictive maintenance capabilities.
You’ll see automation advancements transforming the industry through smart technology integration, enhancing both precision and productivity. Modern systems now offer:
- Real-time monitoring with IoT sensors that adjust cutting parameters automatically, reducing material waste and improving energy consumption
- Machine learning algorithms that analyze cutting patterns and recommend ideal processing sequences based on material properties and geometrical complexities
- Cloud-based remote operation capabilities that enable you to control multiple cutting systems from centralized command centers
These innovations are revolutionizing pipe laser cutting, making it more efficient and cost-effective while maintaining the highest quality standards in precision manufacturing.
Comparing Laser Cutting With Traditional Methods
Since traditional pipe cutting methods like mechanical sawing and plasma cutting have dominated the industry for decades, it’s crucial to understand how laser cutting technology outperforms these conventional approaches. You’ll find that laser cutting delivers superior precision with tolerances as tight as ±0.1mm, while traditional techniques typically achieve only ±0.5mm. When you’re working with complex geometries, laser cutting eliminates the mechanical stress and material deformation common in conventional methods.
The advanced technology of laser cutting also reduces your material waste by up to 30% compared to traditional methods and eliminates the need for secondary finishing operations. You’ll experience faster production speeds, with laser cutting operating at up to 20 meters per minute, considerably outpacing mechanical cutting’s typical 2-3 meters per minute rate.
Conclusion
You’ve witnessed the transformative journey of precision pipe laser cutting, where technological finesse meets industrial artistry. Through your mastery of advanced systems, material optimization, and quality control protocols, you’re now equipped to navigate this sophisticated landscape. As you continue to refine your expertise, you’ll find that laser cutting’s superior accuracy and versatility make traditional methods appear increasingly antiquated in today’s demanding manufacturing environment.