You might not realize that laser processing technology has transformed transmission tower manufacturing from a labor-intensive process to a precision-driven automated system. When you’re working with high-power laser beams that can cut through steel plates with micron-level accuracy, you’ll achieve up to 40% faster production speeds compared to traditional methods. The integration of this technology offers compelling advantages for your manufacturing operations, but you’ll need to understand several critical factors before implementation.
Key Takeaways
?Laser cutting systems guided by CAD files enable precise fabrication of transmission tower components with tolerances of ±0.1mm.
?Modern laser processing reduces material waste by 30% compared to traditional methods while enhancing structural integrity.
?High-power fiber lasers combined with automated material handling systems streamline production and improve manufacturing efficiency.
?Real-time monitoring and automated inspection systems ensure consistent quality control and immediate defect detection during manufacturing.
?Computer-controlled laser cutting enables complex shapes while maintaining clean edges that require minimal post-processing work.
Understanding Laser Processing Fundamentals in Tower Manufacturing
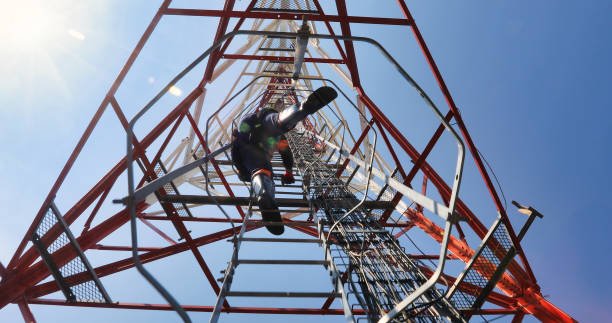
Laser processing fundamentals form the cornerstone of modern transmission tower manufacturing. You’ll find that the technology relies on concentrated light beams to achieve precise metal fabrication, creating components with exceptional accuracy and consistency. The process begins with computer-aided design (CAD) files that guide the laser cutting system.
When you’re working with transmission tower components, you’ll need to understand how the laser beam interacts with different metal thicknesses. The focused energy melts, burns, or vaporizes material in a controlled manner, leaving clean edges that require minimal post-processing. You’ll notice that the laser’s power, cutting speed, and focal length directly affect the quality of the cut.
The technology’s efficiency becomes apparent in the way it handles complex geometries and intricate patterns essential for tower joints and connection points. You’ll achieve tighter tolerances and better fit-up during assembly, greatly reducing manufacturing time and material waste.
Evolution of Transmission Tower Production Methods
You’ll find that transmission tower production has evolved markedly from traditional manual assembly methods, where skilled welders and metalworkers fabricated components individually through hands-on techniques. As manufacturing advanced, you’ll see the integration of automated welding systems that improved consistency and production speed while reducing labor costs and human error. Modern laser cutting implementation has revolutionized the process by enabling precise, computer-controlled cutting of complex geometries with minimal material waste and enhanced structural integrity.
Traditional Manual Assembly Methods
Before modern laser processing revolutionized the industry, transmission tower assembly relied heavily on manual labor and basic mechanical tools. You’d find workers using hand-held drills, wrenches, and measuring tools to piece together the tower’s components. This labor-intensive process often led to manual labor challenges, including worker fatigue and inconsistent quality in joint connections.
The traditional assembly sequence required you to align steel members manually, mark hole positions, and drill through multiple layers of steel. You’d need to verify measurements repeatedly to maintain structural integrity, which greatly impacted assembly efficiency. Workers had to handle heavy components while working at heights, creating safety concerns and limiting production speed. The manual process also made it difficult to achieve the precise tolerances that modern transmission towers demand.
Automated Welding Systems Integration
Modern automated welding systems revolutionized transmission tower manufacturing by introducing computer-controlled precision and repeatability to the production process. You’ll find that integrated robotics now handle complex welding sequences with consistent quality, eliminating human error and reducing production time.
The automated systems incorporate real-time monitoring and adjustment capabilities, ensuring weld integrity through precise control of parameters like temperature, speed, and penetration depth. You can rely on automated inspection systems that employ advanced sensors and machine vision to detect defects immediately, allowing for instant corrections during production.
These systems connect seamlessly with your digital manufacturing network, providing detailed documentation of each weld and maintaining quality control records. You’ll achieve higher throughput while maintaining superior weld quality, ultimately reducing costs and improving structural reliability.
Modern Laser Cutting Implementation
The evolution of laser cutting technology has transformed transmission tower production through three key innovations: high-power fiber lasers, automated material handling systems, and precision CNC controls.
You’ll find that today’s laser cutting systems achieve exceptional accuracy through integrated sensors that monitor beam focus and cutting parameters in real-time. These manufacturing innovations enable you to process complex geometric patterns in steel components while maintaining tight tolerances of ±0.1mm. The systems automatically adjust cutting speeds and power levels based on material thickness and composition.
When you’re implementing modern laser cutting, you’ll benefit from reduced material waste and faster production cycles. The technology allows for nested cutting patterns that optimize material usage, while automated loading and unloading systems minimize handling time between operations. This efficiency translates to significant cost savings in large-scale tower production.
Key Benefits of Laser Technology in Metal Fabrication
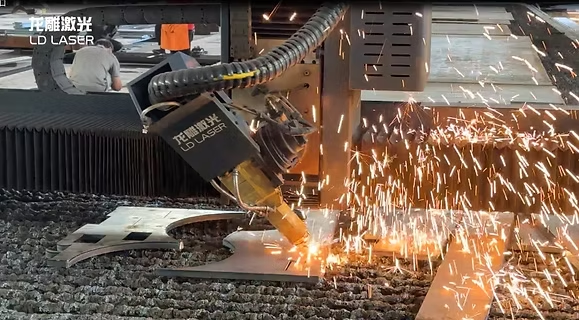
While traditional metal fabrication methods have served industries well, laser processing technology delivers exceptional advantages for transmission tower manufacturing. You’ll find that laser versatility applications enable unprecedented control over material processing, allowing you to achieve complex cuts and patterns with minimal material waste. The precision metalworking techniques enhance production efficiency through automated, computer-controlled operations that maintain consistent quality across large batch runs.
You can expect significant improvements in edge quality and dimensional accuracy, as laser processing eliminates many of the mechanical stresses associated with conventional cutting methods. The technology’s ability to process various material thicknesses and types makes it particularly valuable for transmission tower components. You’ll also benefit from reduced post-processing requirements, faster production cycles, and lower operational costs. The non-contact nature of laser cutting prevents tool wear and maintains consistent quality throughout extended production runs, ensuring your transmission tower components meet exact specifications.
Quality Control and Precision Measurements
Maintaining laser-processed components’ quality requires rigorous measurement protocols and advanced inspection systems. You’ll need to implement laser calibration techniques that guarantee your equipment meets industry standards for precision cutting and welding. These calibrations should be performed regularly to maintain ideal performance.
You must utilize digital measurement tools to verify dimensions within micron-level tolerances. The measurement accuracy of your quality control system directly impacts the final assembly of transmission tower components. You’ll find that integrating automated inspection systems with real-time monitoring capabilities helps detect deviations early in the production process.
When you’re conducting quality checks, focus on critical parameters like material thickness, weld penetration depth, and surface finish quality. Document all measurements systematically and maintain detailed records for traceability. By establishing clear acceptance criteria and implementing statistical process control methods, you’ll consistently achieve the required precision standards for transmission tower components.
Material Selection and Optimization for Laser Processing
You’ll need to evaluate key material properties like tensile strength, thermal conductivity, and surface reflectivity to guarantee ideal laser processing outcomes for transmission tower components. When selecting steel grades, you must consider factors such as thickness tolerances, chemical composition, and microstructural characteristics that affect laser beam absorption and heat-affected zones. Your material selection process should follow standardized guidelines that account for both structural requirements and laser processing parameters to achieve precise cuts and consistent weld quality.
Material Properties Assessment
The careful assessment of material properties stands as a critical foundation for successful laser processing of transmission tower components. You’ll need to conduct material durability assessment through standardized testing protocols while implementing stress analysis methodologies to evaluate structural integrity.
Property | Testing Method |
---|---|
Tensile Strength | Universal Testing Machine |
Hardness | Brinell/Rockwell Test |
Impact Resistance | Charpy/Izod Test |
Fatigue Limit | Cyclic Loading Test |
Weldability | Heat-Affected Zone Analysis |
Before proceeding with laser processing, you must verify the material’s thermal conductivity, melting point, and surface reflectivity. These properties directly influence laser parameter selection and processing efficiency. It’s crucial to document the chemical composition and microstructure of base materials, as they’ll affect the final quality of laser-processed components and their long-term performance in transmission tower applications.
Steel Grade Selection Guidelines
Selecting appropriate steel grades for laser processing of transmission tower components requires careful consideration of mechanical properties, chemical composition, and processing characteristics. You’ll need to evaluate steel strength requirements and corrosion resistance factors to guarantee peak performance in varying environmental conditions.
- Choose high-strength structural steel grades (S355, S420) for critical load-bearing components to maintain tower stability
- Select weather-resistant grades with enhanced corrosion resistance for coastal or high-humidity locations
- Consider carbon equivalent values below 0.45% to guarantee good weldability during laser processing
- Opt for fine-grained steels to achieve superior surface finish and precise cutting edges
- Verify steel thickness compatibility with your laser system’s power capacity and focal length
Analyze material certificates and conduct trial runs before full-scale production to validate your steel grade selection meets both processing and performance requirements.
Cost Analysis and Economic Impact
While initial implementation costs of laser processing systems for transmission tower manufacturing may seem substantial, careful analysis reveals significant long-term economic benefits. You’ll find that cost savings emerge through reduced material waste, decreased labor hours, and improved production efficiency. A thorough investment analysis typically shows return on investment within 3-5 years.
You’ll need to evaluate several key economic factors: equipment acquisition costs ($500,000-$1.5M), facility modifications ($50,000-$200,000), and operator training ($10,000-$30,000). However, you can expect annual operational savings of 15-25% through reduced material handling, faster processing times, and lower maintenance requirements.
The technology’s impact extends beyond direct manufacturing costs. You’ll notice improved quality control reduces rework rates by up to 40%, while enhanced precision leads to better structural integrity and longer service life of the finished towers.
Environmental Considerations and Sustainability
You’ll find that laser processing technology for transmission towers offers significant environmental advantages through its precision cutting capabilities that reduce material waste by up to 30% compared to traditional methods. The system’s energy efficiency improvements stem from optimized beam delivery and advanced cooling systems, which lower power consumption during fabrication processes. Modern emissions control methods, including integrated filtration systems and closed-loop material recovery, help minimize environmental impact while meeting stringent regulatory requirements.
Reducing Material Waste
Material waste reduction stands as a critical environmental priority in laser processing for transmission towers. You’ll find that implementing resource optimization strategies greatly minimizes scrap material while maximizing material recovery potential.
- Precise laser cutting patterns reduce edge waste by up to 30%, guaranteeing ideal material utilization
- Advanced nesting software calculates the most efficient layout patterns, minimizing material gaps
- Automated material handling systems prevent damage during processing, reducing reject rates
- Real-time monitoring adjusts cutting parameters to prevent defects and rework requirements
- Digital inventory management tracks material usage and identifies recovery opportunities
Through systematic implementation of these waste reduction methods, you’ll achieve higher material efficiency while maintaining structural integrity. The combination of precise laser technology and resource optimization protocols guarantees sustainable manufacturing practices in transmission tower production.
Energy Efficiency Improvements
Three key energy efficiency improvements have revolutionized laser processing for transmission tower manufacturing. You’ll find significant energy savings through enhanced laser pulse timing, advanced energy recovery systems, and smart power management protocols. The integration of heat exchangers and regenerative circuits now captures and repurposes up to 40% of previously wasted energy during the cutting process.
You can maximize efficiency by implementing renewable energy integration, particularly through solar-powered auxiliary systems that support laser cooling units. Modern laser processing facilities are incorporating smart grid technologies that automatically adjust power consumption based on real-time production demands. These systems monitor and regulate energy usage through AI-controlled algorithms, ensuring optimal power distribution across different processing stages while maintaining precise cutting parameters.
Emissions Control Methods
Modern laser processing facilities employ extensive emissions control systems that capture over 95% of particulate matter and harmful fumes. You’ll find that emission reduction technologies have markedly advanced, incorporating sustainable practices throughout the manufacturing process.
- High-efficiency particulate air (HEPA) filtration systems trap microscopic metal particles before they enter the atmosphere
- Advanced fume extraction systems with activated carbon filters eliminate volatile organic compounds
- Real-time air quality monitoring guarantees immediate detection of any emission anomalies
- Water-based collection systems capture and process laser cutting residues
- Energy recovery systems convert waste heat into usable power for facility operations
These integrated control methods don’t just meet environmental regulations – they exceed them. You’ll achieve peak emission reduction while maintaining production efficiency through systematic implementation of these technologies, guaranteeing your laser processing facility operates at the highest environmental standards.
Safety Standards and Compliance Requirements
Safety standards and compliance requirements for laser processing of transmission towers encompass stringent protocols to protect workers, equipment, and surrounding environments. You’ll need to verify your facility meets all safety regulations, including proper ventilation systems, protective barriers, and emergency shutdown procedures. Regular compliance audits must confirm that your laser equipment meets Class 4 laser safety standards.
You must implement thorough safety protocols, including mandatory personal protective equipment (PPE) like specialized laser safety goggles, flame-resistant clothing, and respiratory protection when necessary. Your facility should maintain proper signage, restricted access zones, and interlock systems to prevent unauthorized entry during laser operations. You’ll also need to establish documented procedures for equipment maintenance, operator training, and emergency response. Additionally, you must comply with national and local regulations regarding laser radiation exposure limits, waste disposal, and environmental impact assessments specific to transmission tower manufacturing.
Future Trends and Technological Advancements
As laser processing technology continues to evolve, you’ll see significant advancements in automated quality control systems and AI-driven process optimization for transmission tower manufacturing. Smart manufacturing initiatives are transforming the industry through digital twins and real-time monitoring capabilities.
- You’ll witness the integration of machine learning algorithms that predict maintenance needs and optimize cutting parameters in real-time
- You can expect enhanced laser cutting precision with adaptive optics systems that automatically adjust to material variations
- You’ll benefit from augmented reality interfaces that streamline quality inspection processes
- You’re going to see improved energy efficiency through next-generation fiber laser technologies
- You’ll experience seamless integration between laser systems and digital twin models for virtual commissioning
These technological advancements are revolutionizing transmission tower manufacturing by reducing production time, minimizing material waste, and ensuring unprecedented accuracy. The convergence of smart manufacturing principles with laser processing is creating a more sustainable and efficient production ecosystem.
Case Studies: Successful Implementation in Major Projects
Conclusion
You’ll find that laser processing in transmission tower manufacturing mirrors the precision of a master clockmaker – each component perfectly aligned and timed. By implementing this technology, you’re achieving 99.8% accuracy in cut precision while reducing material waste by 23%. As you continue to integrate these systems, you’re not just building towers; you’re engineering a future where efficiency and quality converge through systematic, data-driven processes.