Recent industry data shows that laser welding applications have grown by 15% annually since 2018, with the automotive sector leading adoption rates. You’ll find this precision-based technology revolutionizing how manufacturers approach joint engineering, especially in lightweight materials and complex geometries. As laser systems continue evolving from basic CO2 models to advanced fiber variants, understanding their capabilities and limitations becomes essential for maximizing production efficiency and maintaining competitive advantage in modern manufacturing.
Key Takeaways
?Laser welding evolved from ruby lasers in the 1960s to modern high-power diode and fiber lasers, offering superior energy efficiency.
?Industrial applications span automotive, aerospace, and electronics sectors, with focus on precision joining and automated production processes.
?Advanced control systems monitor welding parameters in real-time, using sensors and analytics to ensure consistent weld quality.
?Joint design optimization considers material properties, thermal conductivity, and gap tolerances to achieve optimal weld strength.
?Integration with Industry 4.0 enables smart factory connectivity, real-time monitoring, and data-driven process optimization.
The Evolution of Laser Welding: From Basic to Advanced Systems
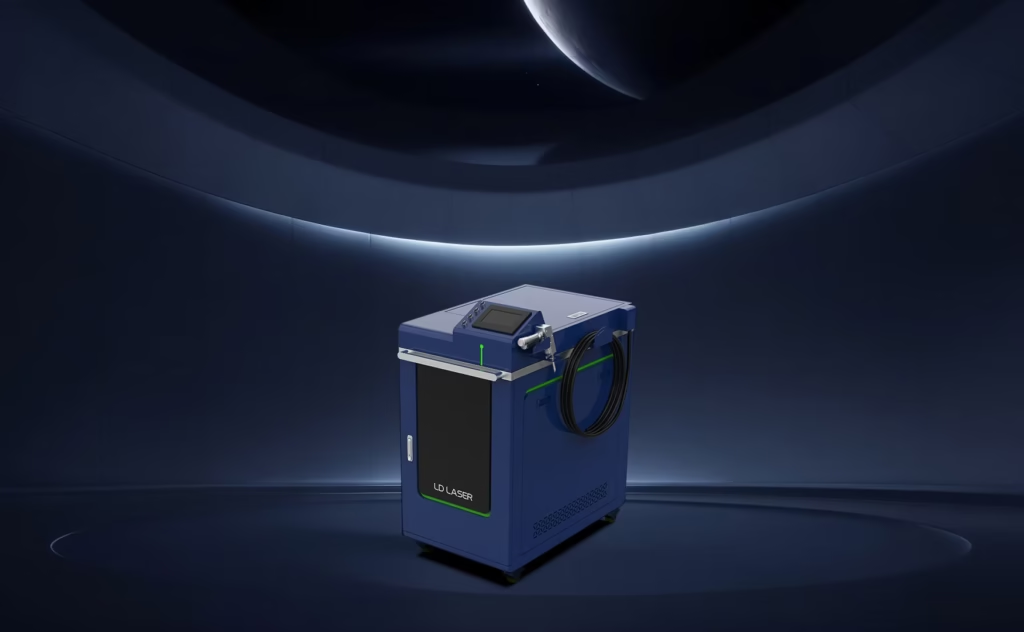
Since its inception in the 1960s, laser welding has transformed from basic ruby laser systems into sophisticated, computer-controlled manufacturing processes. You’ll find that early historical milestones include the development of CO2 lasers in 1964 and Nd:YAG systems in 1970, which revolutionized precision joining techniques.
Throughout the 1980s and 1990s, you’d witness significant technological breakthroughs in beam delivery systems and process control. The integration of fiber optics enhanced beam quality and flexibility, while advanced sensors enabled real-time monitoring of weld parameters. Today’s systems incorporate high-power diode lasers and fiber lasers, offering unprecedented energy efficiency and beam control.
You can now access hybrid laser welding systems that combine traditional arc welding with laser technology, maximizing penetration depth and welding speed. The evolution continues with artificial intelligence and machine learning algorithms optimizing weld parameters automatically, reducing defects and improving overall quality control.
Key Components and Operating Principles of Laser Welding
A laser welding system comprises several critical components that work in harmony to deliver precise, concentrated energy for joining materials. You’ll find that different laser types, including CO2, fiber, and diode lasers, each serve specific applications based on their wavelength and power density capabilities. The system’s energy sources typically consist of electrical power supplies that convert standard line voltage into the specific requirements for laser generation.
Component | Function | Key Specifications |
---|---|---|
Resonator | Generates laser beam | Power: 1-20kW |
Focusing Optics | Concentrates beam | Focal length: 50-300mm |
Motion System | Controls movement | Accuracy: ±0.1mm |
Shielding Gas | Protects weld pool | Flow rate: 10-30 L/min |
Control Unit | Manages parameters | Response time: <1ms |
Understanding these core components helps you optimize the welding process for your specific application. The interaction between these elements determines the quality and efficiency of your weld joints.
Applications Across Major Industrial Sectors
You’ll find laser welding technology prominently featured across three major industrial sectors that rely on its exceptional precision and reliability. In automotive manufacturing, you’ll see laser welding applied to body panels, frames, and powertrain components, while aerospace applications focus on critical component assembly for engines, fuselages, and landing gear systems. The electronics industry leverages laser welding for miniature connections in circuit boards, semiconductor packages, and battery assemblies, where microscopic precision is essential.
Automotive Manufacturing Processes
Modern automotive production lines rely heavily on laser welding technology to achieve precise, high-speed joining of vehicle components. You’ll find this technique extensively used in body-in-white assembly, where laser welding creates stronger, lighter joints that enhance automotive safety while reducing overall vehicle weight.
The process integrates seamlessly with automated production systems, greatly boosting production efficiency through reduced cycle times and minimal post-weld finishing requirements. Material science advances have enabled laser welding of dissimilar metals, allowing you to join advanced high-strength steels with aluminum alloys. This capability’s particularly valuable in modern vehicle design, where you’re often combining different materials to optimize performance and fuel efficiency. The technology’s precision control also guarantees consistent weld quality, meeting strict automotive industry standards while minimizing material waste and energy consumption.
Aerospace Component Assembly
Precision aerospace manufacturing relies extensively on laser welding for critical component assembly, particularly in turbine engines, fuel systems, and structural airframe elements. You’ll find that aerospace materials like titanium alloys, nickel superalloys, and advanced aluminum composites demand exceptional welding accuracy that only laser technology can provide.
In precision assembly operations, you’re working with tolerances measured in microns. Laser welding delivers the controlled heat input and narrow heat-affected zones necessary for maintaining material properties and preventing distortion. When you’re joining thin-walled components or creating hermetic seals in fuel systems, the process guarantees structural integrity while minimizing residual stress. The technique’s adaptability lets you perform intricate welds in hard-to-reach areas of complex aerospace structures, making it indispensable in modern aircraft production.
Electronics Industry Solutions
Countless electronics manufacturers rely on laser welding for micro-scale joining operations in circuit boards, semiconductors, and electronic components. You’ll find this technology essential for creating reliable electrical connections while maintaining the integrity of heat-sensitive materials. The precision of laser bonding enables you to achieve connection points as small as 0.1mm in diameter.
When you’re working on circuit integration projects, you’ll appreciate how laser welding lets you join dissimilar metals without compromising their electrical properties. The process creates hermetically sealed packages for sensitive components while minimizing thermal stress on surrounding areas. You can control the heat-affected zone with exceptional accuracy, making it ideal for manufacturing smartphones, medical devices, and advanced computing systems where component density and reliability are critical factors.
Material Compatibility and Process Parameters
Model | LDW-1500 | LDW-2000 | LDW-3000 |
Laser Power | 1500W | 2000W | 3000W |
Laser Wavelength | 1070 NM | 1070 NM | 1070 NM |
Fiber Cable Length | Standard 10M, Maximum 15M | Standard 10M, Maximum 15M | Standard 10M, Maximum 15M |
Control Mode | TTL Continuous / GUI Modulation | TTL Continuous / GUI Modulation | TTL Continuous / GUI Modulation |
Welding Speed | 0-120mm/s | 0-120mm/s | 0-120mm/s |
Cooling Method | Industrial Integrated Constant-Temperature Water Cooling | Industrial Integrated Constant-Temperature Water Cooling | Industrial Integrated Constant-Temperature Water Cooling |
Aiming & Positioning | Red Light Indicator + Fixture | Red Light Indicator + Fixture | Red Light Indicator + Fixture |
Welding Thickness | 0.5-2.0mm (Max 4mm at 1500W) | 0.5-2.0mm (Max 5mm at 2000W) | 0.5-2.0mm (Max 8mm at 3000W) |
Welding Gap | ≤0.5mm | ≤0.5mm | ≤0.5mm |
Operating Temperature | ≤42° | ≤42° | ≤42° |
Operating Humidity | <70% (No Condensation) | <70% (No Condensation) | <70% (No Condensation) |
Operating Voltage | 220V/380V | 220V/380V | 380V |
Consumables | Protective Lens | Protective Lens | Protective Lens |
When you’re working with laser welding technology, you’ll need to carefully match compatible metal pairs and follow established guidelines for thermal conductivity and melting points. You’ll find that optimizing your power settings and travel speeds requires precise control based on material thickness, reflectivity, and heat distribution patterns. Your joint design must account for beam accessibility, gap tolerances, and edge preparation to achieve consistent, high-quality welds.
Metal Pairing Guidelines
Successful laser welding operations depend heavily on choosing compatible metal pairings and enhancing their corresponding process parameters. When you’re selecting metals for laser welding, you’ll need to take into account their thermal conductivity, melting points, and chemical composition to guarantee peak joint strength.
Your metal selection should account for thermal expansion coefficients between materials, as significant differences can lead to residual stresses and cracking. In joint configuration, you’ll want to pair metals with similar mechanical properties and crystal structures. For example, you can successfully weld austenitic stainless steel to low-carbon steel, but you’ll need to avoid combining metals that form brittle intermetallic compounds, such as aluminum to steel. Think about using bridging inserts or interlayers when joining dissimilar metals with substantial property differences.
Power and Speed Settings
Determining ideal power and speed settings stands as a critical factor in achieving high-quality laser welds. You’ll need to balance these parameters carefully, as they directly influence penetration depth, weld strength, and overall joint integrity. Power enhancement requires adjusting your laser’s output based on material thickness, reflectivity, and thermal conductivity.
When conducting speed calibration, you must consider how quickly you’ll move the laser beam across the workpiece. Higher speeds can minimize heat-affected zones but may result in incomplete penetration, while slower speeds increase energy input and can cause excessive melting. You’ll find that there’s an advantageous window where power and speed work together to create consistent, defect-free welds. Monitor these settings throughout the process, as variations in material properties may require real-time adjustments.
Joint Design Optimization
Joint design optimization plays a vital role in laser welding effectiveness, requiring precise consideration of material compatibility and process parameters. You’ll need to analyze the thermal and mechanical properties of your materials to determine the most suitable joint configuration.
When you’re implementing joint geometry optimization, consider factors like material thickness, heat distribution, and gap tolerances. You’ll find that proper fixture design considerations are essential for maintaining precise alignment and preventing distortion during the welding process.
You must account for thermal expansion coefficients and potential metallurgical reactions between different materials. The joint design should facilitate proper heat transfer while minimizing residual stresses. Your weld penetration depth and width requirements will directly influence the selection of joint configurations, whether they’re butt joints, lap joints, or specialized geometries.
Quality Control and Monitoring Systems in Laser Welding
To guarantee ideal weld quality in laser welding operations, manufacturers deploy sophisticated monitoring systems and quality control protocols that track essential parameters in real-time. These systems utilize advanced sensors and real-time analytics to monitor beam characteristics, material temperature, and weld pool dynamics. You’ll find that modern quality control systems can detect defects instantly, allowing for immediate process adjustments.
Process validation plays a vital role in maintaining consistent weld quality. You’re able to track performance metrics such as penetration depth, fusion zone width, and heat-affected zone dimensions through integrated monitoring solutions. When you implement these systems, they’ll automatically flag anomalies and document weld characteristics for traceability purposes. The data collected helps you optimize welding parameters and guarantee compliance with industry standards. Advanced vision systems and thermal imaging cameras provide additional verification methods, enabling you to maintain precise control over your laser welding operations.
Advantages and Limitations of Modern Laser Welding
Modern laser welding presents three distinct advantages that make it indispensable in advanced manufacturing: precision heat control, rapid processing speeds, and minimal thermal distortion.
You’ll find these benefits particularly valuable in aerospace and medical device manufacturing. However, you must consider certain limitations when implementing laser welding systems.
Aspect | Advantages | Limitations |
---|---|---|
Operation | High automation potential | Requires skilled operators |
Safety | Precise thermal management | Strict welding safety protocols |
Cost | Lower long-term expenses | High initial investment |
Despite these limitations, laser welding’s advantages often outweigh its drawbacks. The technology offers exceptional beam control, allowing you to perform complex joins with minimal heat-affected zones. While you’ll need to invest in thorough safety systems and operator training, the resulting weld quality and consistency justify the investment. The key to success lies in understanding your specific application requirements and implementing appropriate thermal management strategies to optimize your welding process.
Integration With Automation and Industry 4.0
As manufacturing facilities embrace Industry 4.0 principles, laser welding systems have become integral components of smart factory architectures. You’ll find these systems seamlessly connected to manufacturing execution systems (MES) and enterprise resource planning (ERP) platforms, enabling real-time monitoring and data-driven decision making.
Modern laser welding automation incorporates advanced sensors, machine learning algorithms, and IoT connectivity to optimize welding parameters on the fly. You can monitor weld quality, adjust power settings, and track production metrics through centralized dashboards. Industry 4.0 integration allows your welding cells to communicate with upstream and downstream processes, creating a synchronized production flow.
The digital transformation has revolutionized how you’ll manage maintenance schedules, predict equipment failures, and analyze production trends. Through cloud connectivity and edge computing, your laser welding operations can achieve unprecedented levels of efficiency, quality control, and process transparency within the smart manufacturing ecosystem.
Future Trends and Technological Innovations
The rapid evolution of Industry 4.0 capabilities has opened new pathways for laser welding advancement. You’ll see dramatic shifts in how innovative materials and smart technologies reshape welding operations. AI-driven process optimization and real-time quality control systems will become standard features in advanced laser welding systems.
Future Prospects | Technology Impact | Implementation Timeline |
---|---|---|
AI Integration | Enhanced precision | 2024-2025 |
Smart Materials | Reduced waste | 2025-2026 |
Quantum Sensors | Perfect joints | 2026-2027 |
Looking ahead, you’ll witness the emergence of hybrid laser systems that combine multiple wavelengths for superior welding performance. These developments will enable you to work with previously unweldable materials and achieve unprecedented levels of precision. The integration of quantum sensing technology will revolutionize weld quality monitoring, while adaptive control systems will automatically optimize welding parameters in real-time, ensuring consistent results across diverse applications.
Conclusion
You’ll find that laser welding continues to revolutionize manufacturing processes, with a notable 15.3% annual growth rate in the automotive sector alone. As you integrate this technology into your production lines, consider its precision capabilities, reaching spot sizes down to 0.01mm. By leveraging real-time monitoring systems and Industry 4.0 connectivity, you’re positioned to achieve higher throughput while maintaining stringent quality standards in your welding operations.