When Boeing introduced tube laser cutting for their 787 Dreamliner’s structural components, they cut production time by 43% while improving precision to within 0.1mm tolerances. You’ll find this technology isn’t just transforming aerospace – it’s revolutionizing manufacturing across industries. As you explore the capabilities of modern tube laser systems, you’ll discover how precision cutting, automated processing, and smart integration can position your operation at the forefront of manufacturing innovation.
Key Takeaways
Tube laser technology reduces production time by up to 60% through integrated operations and automated workflows.
Advanced quality control systems with real-time monitoring ensure precision and consistency while minimizing defects.
Multi-axis capabilities enable complex geometric cuts and joints in a single pass, eliminating secondary operations.
AI-driven cutting algorithms and smart programming interfaces optimize material usage and reduce waste significantly.
Integration with digital twin technology and cloud analytics enables predictive maintenance and continuous process optimization.
The Evolution of Tube Laser Cutting Technology
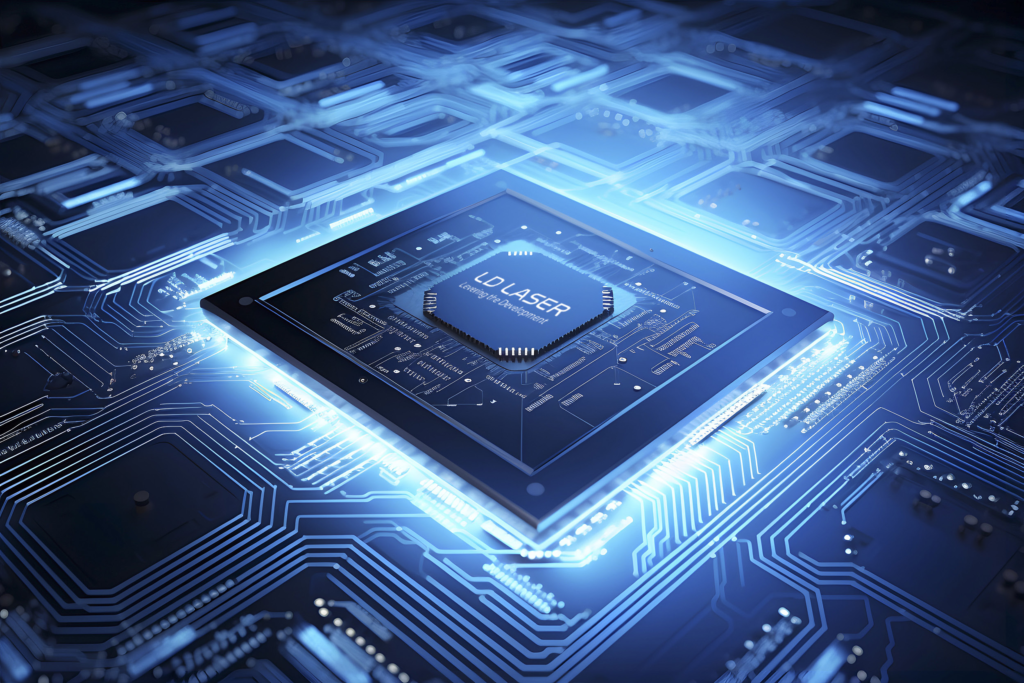
While traditional tube cutting methods dominated manufacturing for decades, the emergence of tube laser technology in the late 1980s revolutionized the metalworking industry. You’ll find that early systems could only process simple geometric shapes, but technological advancements quickly expanded their capabilities.
Key historical milestones include the introduction of 3D cutting heads in the 1990s, allowing for complex angle cuts and bevels. The 2000s brought improved beam quality and power, enabling you to cut thicker materials with greater precision. Today’s systems feature advanced automation, real-time monitoring, and smart programming interfaces. You can now achieve cutting speeds up to five times faster than conventional methods, with minimal material waste and superior edge quality. The integration of fiber laser technology has further enhanced processing capabilities and energy efficiency.
Key Benefits for Modern Manufacturing
When you implement tube laser technology in your manufacturing process, you’ll gain precise control over material quality through automated inspection systems and real-time monitoring capabilities. You can reduce production time by up to 60% compared to traditional methods, as the technology combines multiple operations into a single automated workflow. By optimizing resource allocation through reduced material waste and decreased labor requirements, you’ll achieve significant cost savings while maintaining consistent product quality.
Enhanced Quality Control
Due to its advanced monitoring capabilities, tube laser technology revolutionizes quality control in modern manufacturing operations. You’ll find integrated sensors and real-time analysis systems that continuously monitor cutting parameters, ensuring consistent quality throughout production runs. These systems instantly detect deviations and automatically adjust settings to maintain precision.
The technology’s sophisticated quality assurance protocols enable you to identify potential issues before they become costly defects. You can monitor material thickness variations, edge quality, and dimensional accuracy with microscopic precision. Built-in defect detection algorithms analyze surface finish and structural integrity, flagging any anomalies for immediate attention. Advanced imaging systems verify proper alignment and inspect weld seams, while automated reporting tools generate detailed quality documentation for compliance and traceability purposes.
Production Time Reduction
Because tube laser technology integrates multiple manufacturing processes into a single operation, you’ll experience dramatic reductions in production time compared to traditional methods. By eliminating separate cutting, drilling, and marking steps, you’ll achieve significant process acceleration, often reducing production cycles by up to 60%.
You’ll notice immediate productivity enhancement through automated material handling and reduced setup times. The technology’s ability to perform complex cuts and joints in one pass means you won’t need secondary operations or multiple machine setups. Your programming time decreases substantially as the system’s advanced software optimizes cutting paths and sequences automatically. Additionally, you’ll minimize material handling between workstations, reducing the risk of errors and damage while streamlining your entire production workflow.
Resource Optimization
Through advanced tube laser technology, you’ll enhance resource utilization across multiple manufacturing dimensions. The system’s precise cutting capabilities minimize material waste, while its automated processing reduces labor requirements. You can achieve peak resource allocation by programming multiple jobs simultaneously, maximizing machine uptime and throughput.
The technology enables you to consolidate operations that traditionally required separate machines and operators. You’ll eliminate the need for additional tooling, fixturing, and secondary processing equipment. This consolidation directly impacts your production efficiency by reducing floor space requirements and energy consumption. The integrated quality control features help you minimize defects and rework, ensuring your raw materials and labor hours are utilized effectively. You can also improve inventory management through just-in-time processing capabilities.
Applications Across Different Industries
Tube laser technology’s versatility spans numerous industrial sectors, revolutionizing manufacturing processes across automotive, aerospace, construction, and agricultural equipment industries.
You’ll find automotive applications ranging from exhaust systems to structural frame components, where precise cuts and joints enhance vehicle performance. In medical devices, the technology enables the production of surgical instruments and implants with exceptional accuracy. Furniture design benefits from the ability to create complex geometric patterns and seamless joints. For aerospace components, you can achieve lightweight yet durable structures through precise tube cutting and fitting. The construction materials sector utilizes tube laser technology for architectural elements and structural supports, while the energy sector depends on it for efficient pipeline systems and power plant components.
Cost Analysis and Return on Investment
While these diverse industrial applications demonstrate the technology’s capabilities, understanding the financial implications of tube laser systems represents a key consideration for manufacturers. A detailed cost breakdown reveals that you’ll need to factor in initial equipment costs, maintenance, operator training, and consumables. Your investment timeline typically spans 3-5 years before reaching maximum ROI levels.
- Advanced cutting heads processing multiple materials simultaneously
- Automated material handling systems reducing labor costs
- Smart monitoring systems tracking operational efficiency
- Integrated quality control reducing scrap rates
- Energy-efficient designs lowering utility expenses
You’ll find that modern tube laser systems often deliver faster payback periods through increased productivity, reduced material waste, and lower labor costs. When you analyze the complete financial picture, including reduced inventory and improved product quality, tube laser technology proves cost-effective for most manufacturing operations.
Quality Control and Precision Advantages
You’ll find that tube laser technology dramatically improves quality control through automated inspection systems that can detect defects in real-time. These systems employ advanced sensors and machine vision to verify dimensional accuracy, surface quality, and edge consistency during the cutting process. Your ability to maintain tight tolerances is further enhanced by integrated measurement tools that continuously monitor and adjust cutting parameters to guarantee specifications are met.
Automated Inspection Systems
Advanced inspection systems in tube laser manufacturing integrate sophisticated quality control measures that guarantee unprecedented precision and consistency. You’ll find automated quality protocols that combine real-time monitoring with advanced analytics to detect even microscopic deviations. Modern inspection technology enables immediate corrections and maintains strict adherence to specifications.
- High-resolution cameras capture 360-degree surface analysis
- Laser profilometers measure dimensional accuracy to microns
- AI-powered defect recognition identifies surface imperfections
- Digital twin comparison validates part conformity
- Real-time data logging creates thorough quality reports
These automated systems dramatically reduce human error while increasing throughput. You’re able to verify critical parameters instantly, ensuring each component meets exact specifications before proceeding to the next production phase. The integration of multiple inspection points throughout the process creates a robust quality assurance framework.
Maintaining Dimensional Accuracy
To achieve superior dimensional accuracy in tube laser processing, manufacturers implement precise control mechanisms that maintain tolerances within microns throughout the cutting operation. You’ll need to conduct regular precision calibration checks and maintain strict dimensional consistency across all components.
Parameter | Control Method | Tolerance Range |
---|---|---|
Roundness | Laser scanning | ±0.05mm |
Length | Optical sensors | ±0.1mm |
Wall thickness | Ultrasonic probe | ±0.02mm |
Surface finish | Vision system | Ra 0.8-1.6 |
Your monitoring system must continuously track critical measurements while compensating for thermal expansion and material variations. By implementing real-time feedback loops, you can make immediate adjustments to cutting parameters, ensuring each tube meets exact specifications. This proactive approach notably reduces scrap rates and helps maintain consistent quality across production runs.
Integration With Smart Manufacturing Systems
Modern manufacturing facilities seamlessly integrate tube laser technology into their smart systems through sophisticated automation protocols and networked controllers. You’ll find that data integration enables real-time monitoring and adjustment of cutting parameters, while smart sensors continuously track machine performance and material flow. This interconnected approach maximizes productivity and reduces downtime.
- Advanced PLCs communicate directly with your facility’s MES and ERP systems
- Real-time quality control data flows between inspection stations and the tube laser
- Smart material handling robots synchronize with cutting sequences automatically
- Digital twin technology simulates and optimizes your production processes
- Cloud-based analytics platforms monitor your machine health and performance metrics
Future Trends and Emerging Capabilities
The next decade of tube laser technology promises significant breakthroughs in processing capabilities and operational efficiency. You’ll see advancements in AI-driven cutting algorithms that optimize material usage and reduce waste, aligning with sustainability practices. Multi-axis systems will enable more complex geometries and faster processing speeds, while intelligent monitoring systems will provide real-time quality control.
You can expect developments in processing innovative materials, including advanced composites and hybrid metal alloys. New beam delivery systems will improve precision and reduce energy consumption, while automated tool changing systems will minimize downtime. Machine learning integration will enhance predictive maintenance capabilities and streamline workflow optimization. These emerging capabilities will transform tube laser cutting into a more efficient, sustainable, and versatile manufacturing process that meets evolving industry demands.
Conclusion
You’re standing at the cutting edge of manufacturing evolution, where tube laser technology acts as your precision compass. As you integrate these systems into your smart factory ecosystem, you’ll unleash a treasure trove of efficiency gains and quality improvements. By embracing this technology’s expanding capabilities, you’re not just cutting tubes – you’re sculpting the future of manufacturing with laser-sharp accuracy and data-driven precision.