When you’re cutting intricate aerospace components with multiple internal features, edge accessibility can pose significant challenges, particularly in tight corners and overlapping geometries. You’ll find that traditional approaches often fall short when dealing with complex metal structures that require precise edge quality throughout. While advanced beam delivery systems offer promising solutions, you’ll need to evaluate a thorough strategy that integrates fixture design, motion control, and real-time monitoring to achieve ideal results.
Key Takeaways
Implement multi-axis positioning systems with robotic assistance to reach complex geometries and maintain consistent focal distance during cutting operations.
Utilize advanced beam delivery systems like articulated mirror arms or fiber optics to access confined spaces while preserving beam quality.
Conduct thorough geometry analysis before cutting to identify potential access issues and modify cutting strategies or part design accordingly.
Deploy real-time surface tracking technology to automatically adjust cutting head position based on material variations and surface irregularities.
Design modular fixture systems with adaptive clamping zones to prevent thermal distortion while enabling flexible part positioning.
Understanding Edge Inaccessibility in Laser Cutting Operations
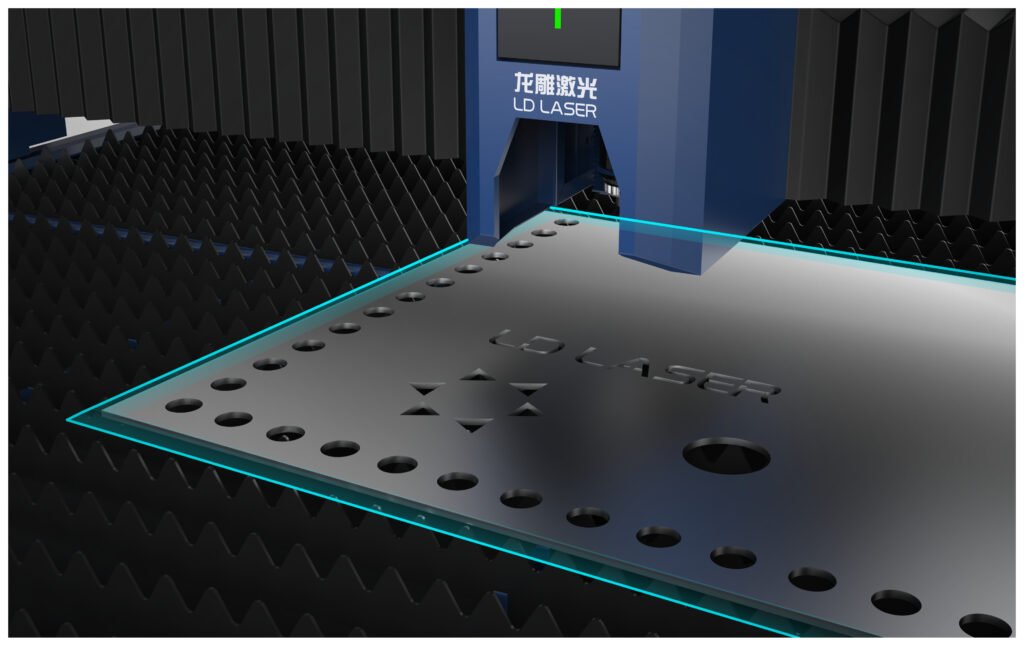
While laser cutting offers exceptional precision for most metal fabrication needs, edge inaccessibility presents a significant challenge that requires careful planning. You’ll encounter edge geometry limitations when your laser cutting head can’t reach certain areas of the workpiece, particularly in complex designs with tight corners or overlapping features.
To identify potential access challenges, you’ll need to analyze your part’s geometry before beginning the cutting process. Critical factors include the standoff distance between the laser nozzle and the material surface, the cutting head’s physical dimensions, and any obstructions that might interfere with the beam path. Understanding these constraints helps you modify your cutting strategy, whether through repositioning the workpiece, adjusting cutting parameters, or redesigning part features to guarantee complete edge accessibility.
Advanced Beam Delivery Systems and Their Impact
You’ll find that modern beam delivery systems offer two primary transmission methods: fiber-based delivery, which excels in flexibility and minimal power loss, and free-space transmission, which provides superior beam quality for specialized applications. Adaptive optics control features now let you dynamically adjust focal length, spot size, and beam characteristics in real-time, maximizing cutting precision across varying material thicknesses. Through advanced beam quality enhancement methods like spatial filtering and wavefront correction, you can achieve near-diffraction-limited performance while maintaining consistent power density at the cutting zone.
Fiber vs. Free-Space Transmission
As laser metal cutting continues to evolve, the choice between fiber and free-space transmission systems considerably impacts cutting precision and operational efficiency. You’ll find that fiber optics deliver superior beam quality and stability, maintaining laser efficiency over longer distances with minimal power loss. The enclosed nature of fiber transmission also protects against environmental interference and contamination.
In contrast, free-space systems offer greater flexibility for specialized applications where direct line-of-sight cutting is required. However, you must account for beam degradation due to atmospheric effects and potential misalignment issues. When selecting between these systems, consider your specific cutting requirements, facility layout, and maintenance capabilities. Modern fiber delivery systems typically provide better overall performance for most industrial applications, though free-space solutions remain valuable for certain niche cutting scenarios.
Adaptive Optics Control Features
Since precision laser cutting demands exceptional beam control, adaptive optics systems represent a significant advancement in beam delivery technology. You’ll find these systems equipped with real-time optical feedback mechanisms that continuously monitor and adjust beam characteristics during cutting operations.
You can enhance your cutting performance through dynamic wavefront correction, which compensates for thermal distortions and mechanical stress in the optical path. The system calibration process involves mapping beam properties across your entire work envelope, ensuring consistent focus and power density at all positions. When you’re working with complex geometries, the adaptive system automatically adjusts focal length and spot size to maintain ideal cutting parameters. This capability proves particularly valuable when you need to cut varying material thicknesses or navigate intricate contours while maintaining edge quality.
Beam Quality Enhancement Methods
While traditional laser systems rely on basic optical components, advanced beam delivery systems incorporate sophisticated enhancement methods to optimize beam quality and cutting performance. You’ll find that modern systems employ multi-stage beam shaping techniques to refine the beam profile, ensuring consistent power distribution across the cutting zone. These systems actively monitor and adjust laser coherence through real-time feedback mechanisms.
To maximize cutting precision, you can implement phase-front correction devices that compensate for atmospheric disturbances and thermal lensing effects. By integrating adaptive beam collimation with dynamic focusing modules, you’ll achieve superior edge quality even on complex geometries. The system’s intelligent monitoring algorithms continuously analyze and optimize beam parameters, maintaining peak performance throughout the cutting process.
Optimizing Fixture Design for Complex Geometries
When designing fixtures for complex laser-cut geometries, you’ll need to strategically position your workpiece support systems to prevent thermal distortion and maintain tight tolerances. You can maximize cutting accuracy by implementing modular clamping zones that adapt to various part configurations while ensuring consistent beam focus height. Your fixture’s clamping zones should incorporate quick-change mechanisms and reference points that enable rapid setup adjustments without compromising dimensional stability.
Workpiece Support Positioning Systems
As laser metal cutting complexity increases, proper workpiece support positioning becomes critical for achieving excellent results. You’ll need to implement multi-axis positioning systems that guarantee superior workpiece alignment throughout the cutting process. Install servo-driven supports with real-time position feedback to maintain positional accuracy within ±0.01mm.
For maximum stability, you should integrate automated height adjustment mechanisms that compensate for material thickness variations. Configure your support points to prevent thermal distortion while maintaining accessibility to all cut edges. Position pneumatic lifters strategically to minimize vibration and deflection during high-speed cutting operations. When dealing with oversized sheets, deploy synchronized support tables that automatically adjust to maintain perfect parallelism with the cutting head.
Modular Clamping Zone Design
The advanced workpiece support system must be complemented by a well-designed modular clamping setup to achieve ideal cutting precision. You’ll need to configure modular fixtures with adjustable clamping zones that can adapt to various workpiece geometries while maintaining consistent pressure distribution. Implement quick-change clamping elements that allow you to reconfigure the setup rapidly between different cutting jobs.
Position your clamping zones strategically to maximize clamping efficiency without interfering with the laser cutting path. Incorporate floating clamp heads that automatically adjust to material thickness variations, ensuring uniform pressure across the workpiece. When dealing with complex contours, utilize stepped clamping arrangements that provide multiple contact points while preventing vibration and material deflection during the cutting process.
Motion Control Strategies for Challenging Edge Access
Despite having advanced laser cutting capabilities, manufacturers often face significant challenges when accessing intricate part edges and complex geometries. You’ll need to implement sophisticated motion control strategies to overcome these obstacles.
Deploy robotic assistance systems with six-axis articulation to reach difficult angles and maintain consistent focal distance. You can enhance precision by integrating real-time surface tracking technology that adjusts the cutting head’s position based on workpiece variations.
Optimize your approach vectors by programming lead-in and lead-out paths that prevent collision while maintaining cut quality. When you’re dealing with tight corners, utilize dynamic acceleration control to adjust cutting speeds automatically. For maximum stability, synchronize the motion control system with laser power modulation, ensuring consistent kerf width even during complex maneuvers.
Real-time Process Monitoring and Adaptive Control
Modern precision laser cutting requires more than just sophisticated motion control – it demands intelligent monitoring systems that can adapt in real-time to changing conditions. You’ll need to integrate multiple sensor types to effectively monitor vital process parameters like beam focus, cutting speed, and material variations.
By implementing thorough laser diagnostics, you can track essential metrics including power stability, beam quality, and cutting depth. Your system should analyze sensor data streams to detect anomalies and automatically adjust cutting parameters. When you’re working with complex edge geometries, real-time monitoring becomes especially critical – helping prevent quality issues before they occur.
You’ll achieve optimal results by combining thermal imaging, plasma detection, and reflection sensors with adaptive algorithms that can fine-tune your laser parameters on the fly.
Material Considerations and Edge Quality Management
When selecting materials for precision laser cutting, you’ll need to account for thermal conductivity, surface reflectivity, and thickness variations that directly impact edge quality. Your material selection criteria should prioritize consistent composition and minimal internal stresses to prevent distortion during cutting.
To achieve ideal edge finish, you’ll want to adjust cutting parameters based on material properties. High-reflectivity metals like aluminum require higher power settings and specialized assist gases, while carbon steels need oxidation control to prevent excessive dross formation. Monitor your cut edge for signs of striation, roughness, or heat-affected zone expansion.
You can improve edge quality by implementing proper focal point positioning, maintaining consistent standoff distance, and using appropriate assist gas pressures for your specific material composition and thickness.
Technological Solutions for Hard-to-Reach Areas
As laser cutting systems encounter intricate geometries and confined spaces, you’ll need specialized technological adaptations to maintain precision. Robotic assistance offers dynamic positioning capabilities, allowing your laser head to navigate complex angles and tight corners with six degrees of freedom. You can integrate advanced optics with flexible beam delivery systems to redirect laser energy into previously inaccessible areas.
To optimize your reach in confined spaces, consider implementing articulated mirror arms or fiber-optic beam delivery systems. These solutions enable precise cutting even in deep cavities or around internal features. You’ll find that combining robotic assistance with specialized focusing optics lets you maintain consistent beam characteristics and kerf width, even when cutting at unusual angles or through restricted access points.
Best Practices for Complex Part Processing
Processing complex parts through laser cutting demands a systematic approach to guarantee the best results. You’ll need to implement strategic planning before beginning any complex cut, carefully analyzing the part geometry and potential stress points.
Start by breaking down intricate designs into manageable segments, establishing a cutting sequence that minimizes material distortion. You should position effective tooling and fixtures to maintain part stability throughout the process. Pay special attention to heat-affected zones and adjust cutting parameters accordingly.
Consider nesting multiple parts to optimize material usage and reduce processing time. You’ll achieve better outcomes by programming appropriate lead-ins and lead-outs for each feature, ensuring clean edges and preventing material waste. Monitor cutting speed and power settings continuously, making real-time adjustments to maintain precision across varying material thicknesses.
Conclusion
You’ll find that mastering edge inaccessibility in laser cutting is like threading a needle through a complex maze – it demands precision and strategic thinking. By implementing advanced beam delivery systems, optimizing fixture designs, and utilizing real-time monitoring, you’re equipped to tackle even the most challenging geometries. When you combine these technical solutions with material-specific considerations, you’ll achieve consistently superior edge quality in hard-to-reach areas.