Just as precision engineering transformed manufacturing in the 20th century, tube laser cutting machines have revolutionized modern metalworking processes. You’ll find these systems combining advanced optics, motion control, and computer automation to achieve cuts that weren’t possible a decade ago. The intricate dance between laser beam generation, material positioning, and real-time adjustments creates a fascinating technical symphony that demands a closer examination of its core principles.
Key Takeaways
Laser cutting machines generate focused beams through CO2 or fiber technology to melt and vaporize material along precise cutting paths.
Rotary axis mechanisms enable 360-degree tube rotation while synchronized motion controls maintain consistent beam focus during cutting.
Beam delivery systems use mirrors and focusing optics to direct and concentrate laser energy onto the tube surface.
Advanced control systems analyze tube structure and material properties to optimize cutting parameters in real-time.
Integrated cooling systems and feedback loops maintain stable energy delivery and prevent thermal damage during the cutting process.
Core Components of Tube Laser Cutting Systems
Tube laser cutting systems consist of several essential components that work in harmony to deliver precise cuts. You’ll find the laser source at the heart of the system, typically utilizing CO2 or fiber technology, which generates the high-powered beam necessary for cutting. The beam delivery system includes mirrors and focusing optics that direct and concentrate the laser onto the workpiece.
The machine’s mechanical structure incorporates a robust tube support system with rotating chuck mechanisms for material handling. Advanced controls manage tube structure analysis and implement material selection criteria to optimize cutting parameters. You’ll also find integrated cooling systems, assist gas delivery mechanisms, and precision motion control components that guarantee accurate positioning. The CNC interface coordinates these elements, while safety enclosures and fume extraction systems protect operators and maintain workplace safety.
Laser Beam Generation and Control Mechanisms
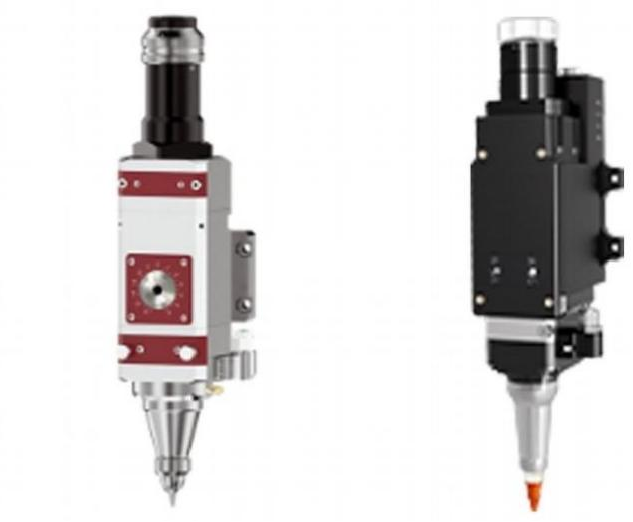
Building upon the core system architecture, the laser beam generation process starts with precise energy excitation within the resonator cavity. You’ll find that controlling laser beam intensity requires sophisticated beam modulation techniques through multiple control points. The system employs mirrors and focusing lenses to direct and concentrate the energy precisely where needed.
Parameter | Control Method | Output Effect |
---|---|---|
Power | PWM Modulation | Energy Density |
Focal Length | Lens Position | Cut Precision |
Pulse Width | Time Control | Heat Impact |
Frequency | Wave Pattern | Material Penetration |
Beam Mode | Spatial Filter | Edge Quality |
The beam control system continuously monitors and adjusts these parameters in real-time, ensuring ideal cutting performance. You’ll achieve consistent results through automated feedback loops that maintain beam stability and precise energy delivery throughout the cutting process.
Material Handling and Loading Operations
When implementing an efficient tube laser cutting system, proper material handling and loading operations serve as critical foundations for successful production. You’ll need to take into account both automated loading systems and material storage solutions to optimize your workflow.
Your automated loading system should incorporate bundle loaders, loading tables, and chain conveyors that can seamlessly transfer tubes from storage to the cutting zone. You’ll want to guarantee your material storage setup includes proper racking systems and sorting mechanisms to accommodate various tube sizes and materials.
To maintain continuous operation, you’ll need to implement buffer zones between your storage area and cutting station. This guarantees you’ve got a steady supply of materials while the machine operates, minimizing downtime during bundle changes and maximizing your production efficiency.
Rotary Axis Technology and Motion Control
Modern rotary axis technology forms the backbone of precise tube laser cutting operations, incorporating sophisticated motion control systems that enable seamless 360-degree rotation of workpieces. You’ll find that rotary axis functionality depends on advanced servomotors and encoders that uphold precise positioning throughout the cutting process.
- High-speed motion control accuracy enables dynamic adjustments during cutting, with real-time compensation for material variations and geometric complexities
- Synchronized movement between the rotary axis and linear drives ensures consistent cutting quality, maintaining beam focus and kerf width across the tube’s surface
- Advanced feedback systems continuously monitor position and velocity, automatically correcting any deviations to uphold cutting precision within microns
The integration of these motion control elements allows you to achieve complex cutting patterns while maintaining tight tolerances and superior edge quality in your tube processing operations.
Beam Focusing and Cutting Parameters
Precise beam focusing mechanisms complement the advanced motion control systems, enabling ideal cutting performance across varying tube diameters and wall thicknesses. You’ll need to adjust the beam intensity and cutting speed based on material properties to achieve favorable results.
Parameter | Effect on Cut Quality |
---|---|
Focus Position | Determines kerf width |
Laser Power | Controls penetration depth |
Gas Pressure | Affects oxidation level |
Focal Length | Impacts beam concentration |
Cutting Speed | Influences edge smoothness |
The focal point’s position relative to the tube surface is critical for achieving clean cuts. You can fine-tune your cutting parameters by maintaining proper standoff distance and adjusting assist gas flow rates. Higher beam intensity typically allows for faster cutting speeds, but you’ll need to balance this against material thickness and composition to prevent thermal damage.
Software and Programming Requirements
Successful tube laser cutting operations require robust CAD/CAM software integration to translate your design specifications into precise machine instructions. You’ll need specialized software packages that can handle both 3D modeling of tubular components and generate optimized cutting paths while accounting for material properties and machine capabilities. The motion control programming system must accurately synchronize the laser beam movements with the tube’s rotation and linear translation, ensuring seamless execution of complex cutting patterns.
CAD/CAM Software Integration
Integration between CAD/CAM software platforms forms the operational backbone of tube laser cutting systems. You’ll need to ascertain seamless software compatibility between your design software and machine control systems to optimize production workflows. Modern CAD capabilities allow you to create complex tubular designs while integrated CAM workflows transform these designs into machine-executable commands.
- Your design optimization process must account for material specifications, cutting parameters, and nesting efficiency to minimize waste and maximize throughput.
- You’ll face integration challenges when connecting different software versions or manufacturers, requiring careful system configuration and regular updates.
- Thorough user training becomes essential as operators need proficiency in both CAD modeling and CAM programming to effectively utilize the integrated system’s full capabilities.
These interconnected software elements directly impact your production efficiency and cut quality.
Motion Control Programming Systems
When implementing tube laser cutting operations, you’ll need robust motion control programming systems that coordinate multiple axes of movement while maintaining precise spatial positioning. These systems rely on sophisticated motion control algorithms to synchronize the laser head’s movement with the tube’s rotation and linear translation.
You’ll need to configure feedback loops that continuously monitor and adjust positioning parameters, ensuring accuracy within microns. The system must process real-time data from encoders and sensors while executing complex cutting patterns. Your programming interface should allow for G-code implementation and custom macro development to handle various tube geometries and cutting requirements.
To maintain peak performance, you’ll need to regularly calibrate the motion control parameters and update the system’s compensation tables to account for mechanical wear and thermal variations.
Quality Control and Precision Measurements
Since precision is paramount in tube laser cutting, implementing rigorous quality control measures and accurate measurement protocols guarantees consistent production standards. You’ll need extensive quality assurance systems that monitor both process parameters and final output specifications. Advanced measurement techniques, including laser scanning and coordinate measuring machines (CMM), help you maintain tight tolerances.
- Monitor dimensional accuracy using high-precision digital calipers and micrometers while checking for deviations from CAD specifications
- Perform regular calibration of measurement tools and verification of laser alignment using interferometry to guarantee consistent cutting performance
- Document quality metrics through statistical process control (SPC) charts, tracking key variables like surface roughness, kerf width, and geometric tolerances
These systematic checks enable you to detect and correct potential issues before they affect production quality.
Safety Features and Operating Protocols
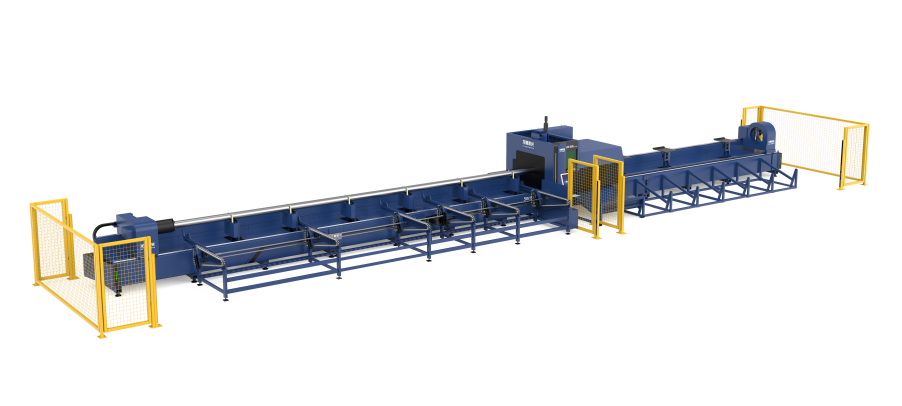
You’ll find emergency stop systems strategically positioned around tube laser cutting machines, providing instant power shutdown capabilities during critical situations. Your protective equipment requirements include safety glasses with appropriate optical density ratings, heat-resistant gloves, and flame-retardant clothing when operating these high-powered systems. When you’re following standard operating protocols, you must verify that all safety interlocks are functional and that emergency stop buttons remain unobstructed before initiating any cutting operations.
Emergency Stop Systems
Emergency stop systems serve as critical safety mechanisms on tube laser cutting machines, providing operators with immediate shutdown capabilities during hazardous situations. These systems integrate multiple emergency protocols to guarantee swift response times and extensive machine deactivation when you encounter potentially dangerous conditions.
- You’ll find emergency stop buttons strategically positioned around the machine, including the control panel, loading zones, and processing areas, allowing quick access during critical moments.
- When activated, the system triggers a series of safety procedures that instantly cut power to laser components, motion systems, and auxiliary equipment.
- After activation, you must follow specific reset protocols to restore machine operations, making sure to conduct thorough safety checks before resuming work.
The redundant nature of these emergency systems provides multiple layers of protection, greatly reducing the risk of accidents and equipment damage.
Protective Equipment Guidelines
Building upon the emergency stop mechanisms, proper protective equipment and safety protocols form the backbone of safe tube laser cutting operations. You’ll need to comply with established safety standards by wearing appropriate protective gear, including laser-safe goggles rated for your machine’s wavelength, flame-resistant clothing, and steel-toed boots.
Your workspace must maintain strict protective measures, including laser curtains or barriers around the cutting area to prevent beam reflection and scatter. You’re required to install proper ventilation systems to extract fumes and particles generated during cutting. Additionally, you should implement a lockout-tagout procedure when performing maintenance, and guarantee all operators receive thorough safety training. Keep your protective equipment regularly inspected and replace any damaged items immediately to maintain ideal safety conditions.
Maintenance and Performance Optimization
Proper maintenance and enhancement of tube laser cutting machines are crucial factors that directly impact operational efficiency, cut quality, and equipment longevity. You’ll need to implement a thorough preventive maintenance schedule and regular performance tuning to guarantee ideal operation.
- Schedule weekly inspections of optical components, including mirrors and lenses, to prevent degradation of laser beam quality and maintain precise cutting capabilities.
- Monitor and adjust assist gas pressure, nozzle condition, and beam alignment monthly to maximize cutting performance and reduce material waste.
- Perform quarterly calibration of motion control systems, including linear guides and servo motors, while documenting all maintenance activities in a detailed log for tracking machine performance trends.
Applications Across Different Industries
Tube laser cutting machines serve as indispensable tools in automotive manufacturing, where you’ll find them creating precise chassis components, exhaust systems, and structural frame elements. In construction and architecture, these machines excel at producing complex support structures, handrails, and decorative elements that require consistent quality and geometric accuracy. Your medical equipment production benefits from tube laser cutting’s ability to fabricate intricate surgical instruments, medical device components, and specialized equipment that demands strict adherence to safety and precision standards.
Automotive Manufacturing and Design
In today’s automotive manufacturing sector, tube laser cutting machines play an essential role in fabricating precise components for vehicle frames, exhaust systems, and structural reinforcements. You’ll find these machines delivering unmatched precision manufacturing capabilities that revolutionize automotive design processes and production efficiency.
When you’re working in automotive manufacturing, you’ll benefit from these key advantages:
- Rapid prototyping capabilities that allow you to test design iterations quickly, reducing development cycles by up to 60%
- Complex geometrical cuts that weren’t possible with traditional methods, enabling innovative structural solutions
- Automated processing that guarantees consistent quality across high-volume production runs while minimizing material waste
These capabilities empower you to meet strict safety standards and lightweight design requirements while maintaining structural integrity in modern vehicle construction.
Construction and Architecture Applications
Modern construction and architecture sectors have adopted tube laser cutting technology from automotive successes to revolutionize structural design and fabrication processes. You’ll find this technology enabling precise cutting of complex tube structures for building frameworks, support systems, and decorative elements.
In architectural designs, you can now create intricate geometric patterns and joints that weren’t feasible with traditional cutting methods. The technology allows you to produce custom-fit tubular components for curtain walls, railings, and structural supports with minimal material waste. You’re able to achieve tight tolerances and perfectly matched connections, essential for modern building aesthetics and structural integrity. The precision cutting capabilities guarantee that your tube structures meet exact specifications, reducing assembly time and improving overall construction quality.
Medical Equipment Production
Leading medical manufacturers leverage tube laser cutting machines for producing essential healthcare equipment and surgical instruments. You’ll find these advanced systems enabling medical device innovation through their ability to create intricate components with exceptional accuracy and repeatability.
- Precision engineering capabilities allow you to manufacture complex medical instruments like endoscopes, surgical scissors, and biopsy forceps with tolerances as tight as ±0.05mm
- You can achieve clean, burr-free cuts on biocompatible materials such as stainless steel and titanium tubes, essential for implantable devices and surgical tools
- The non-contact cutting process guarantees sterility requirements are met while maintaining material properties, critical for medical-grade components that will be used in patient care
These machines continue transforming medical equipment production through automated, high-precision manufacturing processes.
Conclusion
Like a precision conductor orchestrating a symphony of light and motion, you’ll find that tube laser cutting machines represent the pinnacle of modern manufacturing technology. You’ll need to master their intricate components, from beam generation to rotary control systems, to achieve peak results. By understanding these fundamental principles, you’re equipped to leverage this technology’s full potential across diverse industrial applications.