Just as the legendary Archimedes discovered the perfect fulcrum point, you’ll find laser cutting precision hinges on the critical power-thickness equation: P = k × t. When you match your laser’s power output precisely to material thickness, you’ll achieve cleaner edges, narrower kerfs, and tighter tolerances. The coefficient k varies dramatically across materials—from 500 W/in for mild steel to 2,000 W/in for aluminum—demanding careful calibration of your system parameters. The subsequent sections reveal how these calculations transform challenging cuts into manufacturing advantages.
Key Takeaways
- Precision cutting requires calculating optimal power using P = k×t where k is 100-200W/mm for carbon steel.
- Higher wattage enables faster cutting speeds on thicker materials, with power requirements increasing non-linearly with thickness.
- Position the focal point in the upper third for thin materials and adjust dynamically for varying thicknesses.
- Monitor and adjust for material inconsistencies as small as 0.008mm to maintain precise kerfs.
- AI-driven adaptive control systems can adjust parameters within microseconds, maintaining tolerances of ±0.005mm.
Understanding the Core Variables of the Power Thickness Equation
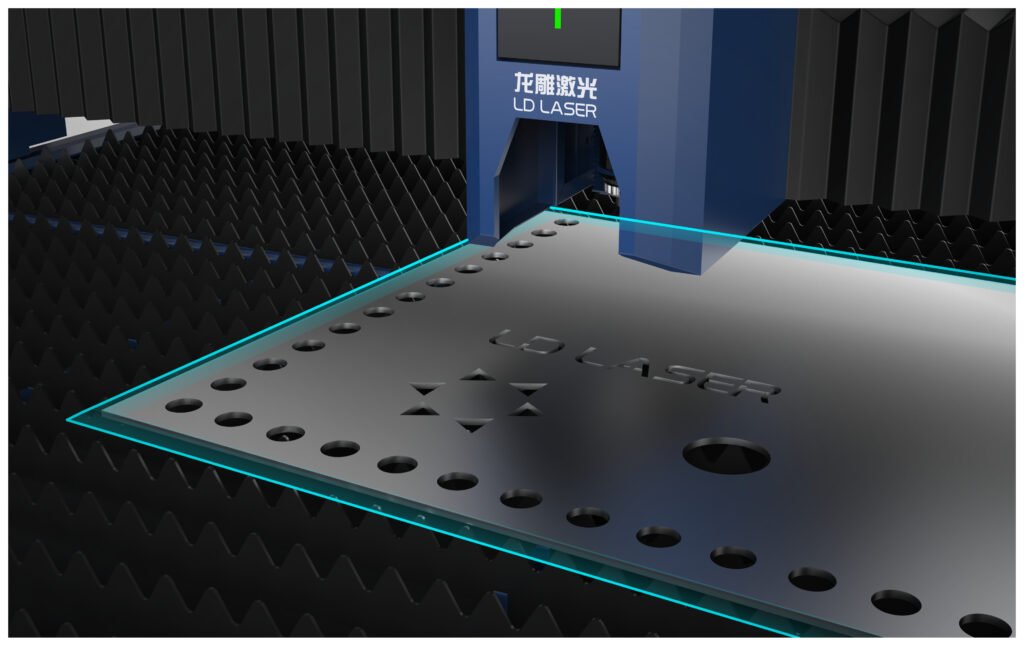
Every competent laser operator must understand the fundamental relationship between laser power and material thickness for achieving ideal cut quality. The power-thickness equation, expressed as P = k × t, where P represents laser power in watts, t signifies material thickness in millimeters, and k denotes the material-specific coefficient, establishes the baseline for operational parameters. Power variations directly influence penetration depth and kerf width, with higher wattage enabling faster cutting speeds on thicker substrates.
You’ll need to calibrate your power settings precisely to maintain cutting efficiency across varying material compositions. For carbon steel, the best power-to-thickness ratio typically ranges between 100-200 watts per millimeter, depending on assist gas pressure and nozzle configuration. When processing aluminum or stainless steel, you must account for thermal conductivity differences by adjusting the coefficient value accordingly. Understanding these variables enables systematic optimization of your cutting parameters rather than relying on trial-and-error approaches.
The Physics Behind Optimal Power-to-Thickness Ratios
While understanding the contextual power-to-thickness relationship provides operational guidelines, the underlying physics explains why these ratios exist in the first place. Laser cutting efficiency fundamentally depends on laser intensity—the power delivered per unit area—which must exceed the material’s ablation threshold. When you increase material thickness, you’re requiring the beam to maintain sufficient energy throughout a longer cutting path.
Energy absorption follows the Beer-Lambert law, where intensity decreases exponentially as light penetrates deeper into material. This physical principle necessitates that power must increase proportionally—but not linearly—with thickness. The ideal ratio varies by material: metals require higher power-to-thickness ratios due to their reflectivity and thermal conductivity, while polymers often need lower ratios but precise wavelength matching. You’ll find that doubling material thickness typically requires 2.3-2.7 times more power, reflecting the combined effects of beam divergence and thermal dissipation throughout the kerf.
Calculating Minimum Power Requirements for Different Materials
When calculating the minimum power requirements for different materials, you’ll need to account for power density factors that determine how concentrated energy must be to initiate cutting. The material’s thermal conductivity, specific heat capacity, and vaporization temperature collectively establish baseline power thresholds, which vary considerably between metals (requiring 1,000-5,000 W), plastics (500-1,500 W), and composites (1,200-3,000 W). Your calculations must incorporate material thickness as a primary variable, following the general rule that power requirements increase non-linearly—typically by a factor of 1.5 to 2.0 for each doubling of material thickness.
Power Density Factors
To calculate minimum power requirements for laser cutting operations, you’ll need to understand the complex relationship between power density and material properties. Power density, measured in watts per square centimeter, determines the amount of energy that can be delivered to a specific area of your workpiece. Materials with high energy absorption coefficients require less power density to achieve effective cuts compared to reflective materials that scatter incident laser energy.
- Beam diameter directly impacts power density, with smaller focal spots creating higher power density for the same wattage
- Material thermal conductivity affects required power density, as heat-dissipating materials demand higher energy concentrations
- Surface reflectivity coefficients must be factored into calculations, particularly for metals like aluminum (up to 98% reflectivity)
- Material thickness follows a non-linear relationship with required power density, often requiring exponential increases for linear thickness changes
Material Thermal Properties
Material thermal properties form the foundation for accurate power requirement calculations in laser cutting applications. To determine minimum power requirements, you’ll need to analyze both the thermal conductivity and material density of your workpiece. These properties directly influence heat dissipation rates and energy absorption during the cutting process.
Material | Thermal Conductivity (W/m·K) | Density (kg/m³) |
---|---|---|
Steel | 43-58 | 7,850 |
Aluminum | 205-250 | 2,700 |
Titanium | 17-22 | 4,500 |
When calculating power requirements, consider that materials with high thermal conductivity dissipate heat more quickly, necessitating increased laser power. Similarly, materials with greater density require more energy to reach melting temperature. You can determine the minimum power (P) using the equation P = k·d·t·v, where k represents thermal conductivity, d equals density, t is material thickness, and v denotes cutting speed.
Thickness-Power Correlations
The precise correlation between material thickness and minimum power requirements establishes a critical foundation for successful laser cutting operations. You’ll find that properly calculated power-to-thickness ratios directly impact cut quality, kerf width, and production efficiency. When determining ideal settings, you must consider how material composition affects absorption rates and thermal conductivity.
- Calculate minimum power (watts) by multiplying material thickness (mm) by the material-specific coefficient (typically 100W/mm for mild steel, 120W/mm for stainless steel).
- Increase power requirements by 15-20% when cutting highly reflective materials like aluminum or copper.
- Adjust cut settings downward for materials with lower melting points, using the thermal conductivity ratio.
- Compensate for alloyed materials by testing at 10% power increments from the calculated baseline.
Speed Optimization: Balancing Throughput With Cut Quality
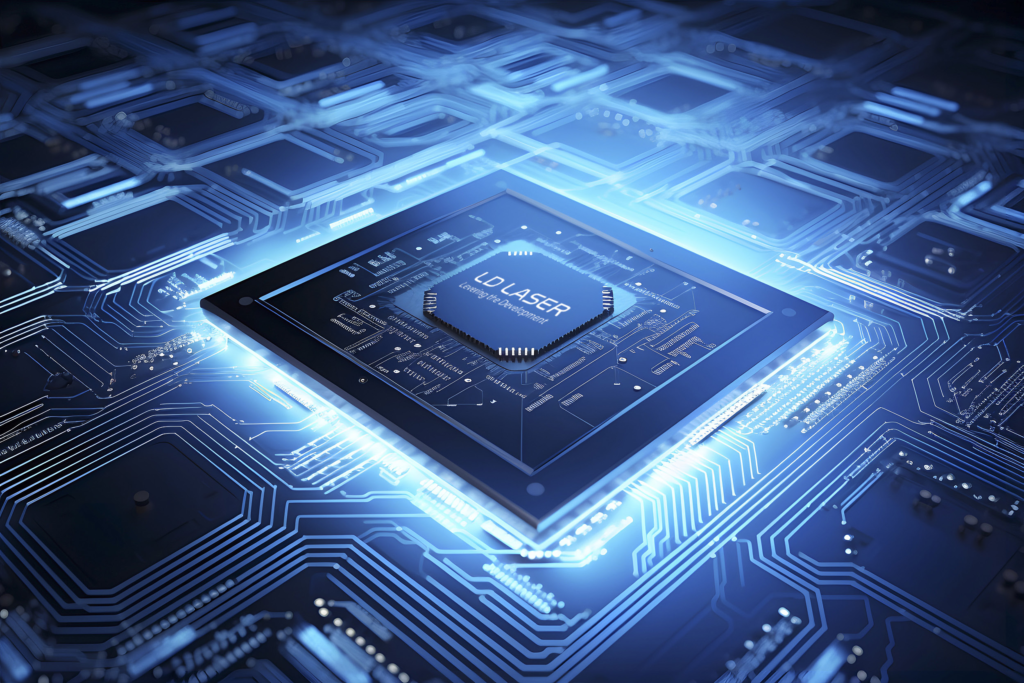
When configuring laser cutting operations, speed settings represent one of the most critical parameters that directly impact both productivity and cut quality. You’ll need to evaluate speed efficiency against quality trade-offs to determine ideal processing rates. As cutting speed increases, your throughput improves, but heat-affected zones may develop irregularly, leading to potential edge defects.
For mild steel (3-6mm), maintain speeds between 2.5-4.0 m/min with proportional power adjustments to preserve edge quality. Carbon steel typically requires 15-20% slower speeds than equivalent stainless steel thicknesses due to different thermal conductivity properties. You can identify ideal speed by examining kerf width consistency—speeds that are too high produce irregular kerfs measuring >0.2mm in variation across a 300mm cut length.
Test cuts at incremental speeds (±0.5 m/min) will help establish your specific material’s threshold point where diminishing returns in quality occur relative to throughput gains.
Beam Focus Considerations for Variable Material Thicknesses
While proper speed settings establish the foundation for quality laser cutting, achieving ideal beam focus across varying material thicknesses requires precise optical adjustments that directly influence cut precision and edge quality. You’ll need to account for beam divergence effects as the laser passes through different material densities, which necessitates strategic focus positioning relative to the workpiece surface. The focal point location determines where energy concentration reaches maximum intensity, critically affecting kerf width and edge perpendicularity.
- Position your focal point at the material’s upper third for thin materials ( mm) to minimize top-edge melting while maintaining sufficient penetration energy
- **Adjust focal length dynamically when cutting variable-thickness components to maintain consistent *energy density* throughout the cut path**
- Implement automated focus adjustment techniques with capacitive or optical sensors for real-time focus correction during processing
- Consider beam mode quality (TEM) when determining prime focus settings, as higher-order modes exhibit different divergence characteristics
Practical Applications: Case Studies in High-Precision Manufacturing
Examining real-world implementations reveals compelling evidence for the critical importance of precision laser cutting techniques across multiple industries. Consider the aerospace component manufacturer that reduced tolerance variations from ±0.15mm to ±0.02mm by implementing adaptive focus control systems, resulting in 99.8% parts acceptance rates. Their precision engineering protocols now serve as industry benchmarks for critical flight components.
You’ll find similar results in medical device manufacturing, where a stent producer achieved 5-micron accuracy through synchronized power-thickness modulation techniques. This advancement simultaneously increased manufacturing scalability by 340% while maintaining dimensional stability across production batches. The power-thickness relationship was continuously monitored via closed-loop control systems, adjusting in real-time to material inconsistencies as minimal as 0.008mm. Such case studies demonstrate that when you properly calibrate laser parameters according to material properties, you can achieve exceptional precision while maintaining production efficiency—the ultimate goal in high-volume manufacturing environments.
Troubleshooting Common Precision Issues Using the Equation
Despite the complexity of precision laser cutting, most common issues can be systematically resolved using the fundamental power-distance-absorption equation: P = D²A/k, where P represents power delivery (watts), D is focal distance (mm), A signifies material absorption coefficient, and k functions as the calibration constant. You’ll find this equation invaluable when diagnosing suboptimal cut quality issues in your operations.
- Inconsistent kerf width – Recalculate required power using P = D²A/k while maintaining consistent focal distance; excessive power creates wider, less precise cuts.
- Edge roughness – Adjust the focal distance (D) while compensating with appropriate power adjustments to maintain thermal equilibrium at the cutting zone.
- Incomplete penetration – Verify material absorption coefficient (A) accuracy for your specific material and increase power accordingly.
- Thermal distortion – Reduce power delivery and increase cutting speed while maintaining the P = D²A/k relationship to optimize laser settings for heat-sensitive materials.
Future Innovations in Power-Thickness Optimization Technologies
You’ll soon witness revolutionary AI-driven adaptive control systems that can dynamically adjust laser parameters within microseconds based on real-time material analysis, eliminating up to 97% of current precision errors. Quantum processing applications will transform power-thickness calculations through simultaneous multi-variable optimization, enabling precise cuts in heterogeneous materials that currently require multiple passes. These emerging technologies will effectively solve the n-dimensional optimization problem inherent in laser cutting, where power, speed, focus, and material properties must be perfectly balanced for submicron precision.
AI-Driven Adaptive Control
How precisely can laser cutting systems respond to material variations in real time? AI-driven adaptive control represents the next frontier in precision laser cutting, incorporating sophisticated adaptive algorithms that continuously monitor and adjust operational parameters. These systems utilize multi-layered neural networks to process control feedback from thermal sensors, high-speed cameras, and acoustic monitors, enabling microsecond adjustments to power and focal position.
- Real-time material density mapping allows for power modulation at 0.1% increments across variable workpieces
- Multi-parameter optimization balances 7+ variables simultaneously, maintaining ±0.005mm tolerances
- Predictive thermal modeling anticipates heat accumulation effects 200-500ms before they manifest
- Self-learning capability reduces setup time by 78% while improving cut quality by analyzing previous operations
Quantum Processing Applications
While AI-driven adaptive systems represent current cutting-edge technology, quantum processing heralds a transformative leap in laser cutting precision beyond classical computational limits. You’ll witness unprecedented computational capabilities as quantum entanglement enables simultaneous processing of multiple power-thickness variables, delivering optimization solutions 1,000 times faster than conventional methods. This quantum advantage translates to sub-micron precision (±0.5μm) even in high-speed cutting operations exceeding 30m/min.
Recent photonic applications integrate directly with quantum processors, creating seamless shifts between computational and physical laser systems. The practical implementation involves quantum sensors that detect material variations at the atomic level, adjusting power delivery within nanoseconds. Your cutting operations will benefit from these advancements through significant reductions in kerf width variations (up to 85% improvement) and virtually eliminated heat-affected zones in thermally sensitive materials.
Conclusion
You’ll maximize laser cutting precision by mastering the power-thickness equation, implementing precise material-specific ratios, and utilizing adaptive focus control. You’ll achieve tighter tolerances through systematic power calibration, speed optimization, and real-time parameter adjustment. By balancing these variables according to P = k × t, you’ll overcome common precision challenges, improve edge quality, and position your operations to benefit from emerging optimization technologies in advanced manufacturing environments.