Laser cutting processes generate microscopic particles as small as 0.1 microns that can bypass standard filtration systems and infiltrate human lung tissue. You’ll need to understand the complex relationship between particle dynamics, airflow patterns, and filtration efficiency to enhance your dust removal system. Modern extraction solutions combine advanced sensing technology with variable-speed controls to maintain ideal collection rates while reducing energy consumption – but selecting the right configuration requires careful analysis of multiple parameters.
Key Takeaways
?Maintain air velocity between 3,000-4,000 feet per minute at capture points while creating negative pressure zones to prevent contaminant dispersion.
?Install multi-stage filtration systems combining pre-filters, HEPA filters, and activated carbon layers to achieve 99% particle capture efficiency.
?Monitor filter differential pressure daily and replace filters every 2,000-3,000 operating hours to maintain optimal system performance.
?Implement VFDs and smart controllers with automated threshold responses for precise power management and enhanced energy efficiency.
?Position intake ports strategically and verify proper airflow dynamics through continuous monitoring of particle concentrations and flow rates.
Understanding Dust and Smoke Composition in Laser Cutting

When laser cutting materials like metals, plastics, or composites, the thermal interaction between the laser beam and workpiece generates a complex mixture of particulate matter and gaseous emissions. You’ll find that smoke particles vary in size from submicron to several microns, while dust properties depend largely on the material being processed. The chemical composition of these byproducts directly correlates to material interaction with the laser beam.
Understanding contaminant sources is essential for system design. During laser operation, you’ll encounter both primary particles from direct material vaporization and secondary formations through chemical reactions. Byproduct analysis reveals that particle size distribution typically follows a bimodal pattern. You must consider health hazards when designing removal systems, as these particles can pose respiratory risks. Your system needs to meet emission standards for workplace safety, which often require filtration of particles down to 0.3 microns. This knowledge helps you optimize capture efficiency and filter selection.
Key Components of Modern Extraction Systems
Modern extraction systems integrate three critical subsystems: filter assemblies with specialized media ranging from mechanical pre-filters to HEPA elements, high-performance centrifugal fans with variable frequency drives, and digital control interfaces with real-time monitoring capabilities. You’ll find these components working in concert to maintain ideal airflow rates, with the filtration media capturing particles down to 0.3 microns and the extraction fans providing adjustable suction forces of 2000-5000 m³/h. The system’s intelligent controls continuously measure filter saturation levels, maintain preset negative pressure parameters, and alert operators when maintenance thresholds are reached.
Filter Types and Media
Effective laser cutting extraction systems rely on multiple filter types and specialized media to capture particles of varying sizes. You’ll find pre-filters that handle larger particulates, followed by main filters utilizing pleated media or cartridge configurations. HEPA filters, rated at 99.97% filter efficiency for particles down to 0.3 microns, serve as the final filtration stage.
Your media options include polyester, cellulose, or synthetic blends, each optimized for specific contaminants. Activated carbon layers absorb gases and odors, while specialized nano-fiber coatings enhance particle capture. To maximize media lifespan, you’ll need to take into account factors like pulse-cleaning capability, material loading capacity, and air-to-media ratio. Modern systems often incorporate differential pressure monitoring to indicate when filter replacement is necessary.
Extraction Fan Technology
High-performance extraction fans serve as the core driving force in laser cutting dust removal systems. You’ll find that modern extraction fans utilize direct-drive motors with variable frequency control, enabling precise adjustment of fan performance based on your system’s demands.
When selecting extraction fans, you need to take into account airflow capacity, static pressure ratings, and power efficiency metrics. Today’s fans incorporate advanced impeller designs with backward-curved blades that enhance extraction efficiency while reducing energy consumption. You’ll achieve ideal results by matching the fan’s specifications to your specific cutting requirements and filtration setup.
The latest fan technologies feature integrated monitoring systems that’ll alert you to performance changes and maintenance needs. These smart systems help you maintain consistent airflow rates and guarantee your dust extraction system operates at peak efficiency.
Control and Monitoring Systems
While manual operation was once the norm, today’s dust extraction systems rely on sophisticated control and monitoring components that integrate seamlessly with your laser cutting machinery. Through sensor integration, you’ll maintain peak airflow parameters and filtration efficiency in real-time, ensuring consistent performance during cutting operations.
Your system’s automated monitoring capabilities will track particle concentrations, pressure differentials, and filter loading status, triggering automated responses when parameters exceed preset thresholds. You’ll receive instant alerts through the machine interface panel when maintenance is required or system efficiency drops below acceptable levels. Advanced control systems also enable you to adjust extraction power based on specific cutting parameters, material types, and production schedules, maximizing energy efficiency while maintaining effective dust and fume removal.
Airflow Dynamics and Collection Efficiency
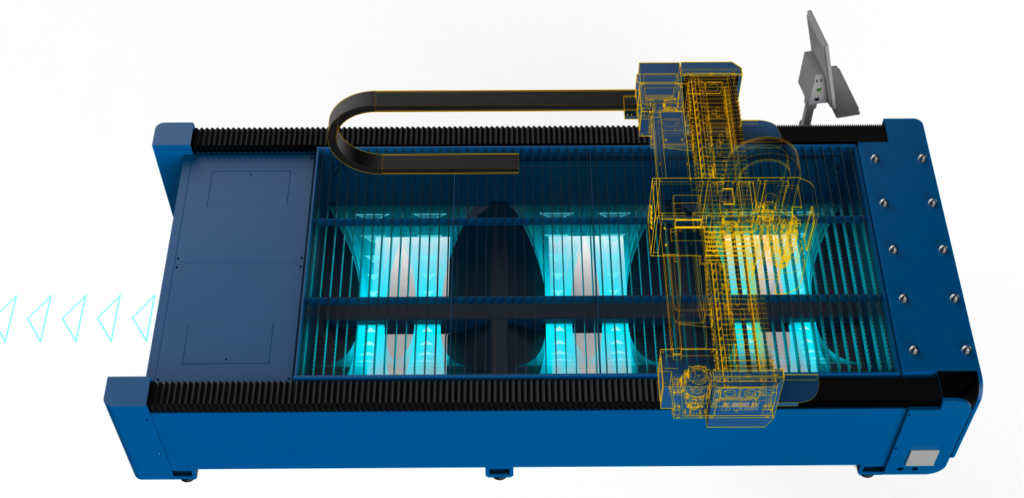
Understanding airflow dynamics is critical in achieving ideal dust and smoke collection in laser cutting systems. You’ll need to analyze airflow patterns across the cutting zone to optimize collection mechanisms and minimize particle escape. The system’s efficiency depends on maintaining proper air velocity, typically 3,000-4,000 feet per minute at capture points.
You’ll find that collection efficiency improves when you position intake ports strategically around the cutting area. Your system should create a negative pressure zone that draws particles toward collection points while preventing turbulent flow that could disperse contaminants. It’s crucial to monitor both laminar and turbulent flow characteristics to maximize particle capture.
To boost collection rates, you’ll want to maintain balanced pressure differentials throughout the system. You can achieve this by adjusting damper settings and ensuring proper duct sizing. Your collection efficiency should reach at least 99% for particles larger than 0.3 microns when the system is properly optimized.
Filtration Technologies and Material Selection
You’ll need to evaluate filter media compositions ranging from polyester and cellulose blends to advanced synthetic materials like PTFE-coated membranes for ideal particle capture efficiency. Your testing protocols should measure key performance metrics including pressure drop, particulate removal efficiency (>99% for PM2.5), and filter loading capacity under varying operational conditions. Regular assessment of maintenance intervals and replacement schedules becomes critical, as filter degradation directly impacts system performance and operational costs.
Filter Media Composition Analysis
Filter media composition plays a critical role in capturing laser cutting particulates across different size ranges. You’ll find that ideal filter effectiveness depends on the specific layering and material combinations selected for your filtration system. The material durability directly correlates with the fiber composition and manufacturing process used.
Key compositional elements include:
- PTFE (polytetrafluoroethylene) membrane layers for submicron particle capture
- Spunbond polyester support structures for mechanical strength
- Meltblown polypropylene for enhanced particle retention
- Activated carbon impregnated layers for VOC absorption
When analyzing filter media composition, you must consider the particle size distribution of your specific cutting application. The media’s porosity, fiber diameter, and layer thickness will determine its collection efficiency and pressure drop characteristics. Select materials that maintain structural integrity under high-temperature exposure and chemical interactions from cutting emissions.
Performance Metrics and Testing
Evaluating filtration system performance requires rigorous testing across multiple standardized metrics. You’ll need to measure particle capture efficiency, pressure drop, filter loading capacity, and exhaust air quality to establish baseline performance benchmarks. Your system evaluations should include both static and dynamic testing conditions that reflect real-world laser cutting operations.
Monitor filter differential pressure and flow rates continuously during testing to assess system stability. You’ll want to track particle size distribution before and after filtration using calibrated aerosol spectrometers. Test your system’s performance with various materials and cutting parameters to validate its effectiveness across different scenarios. Verify you’re documenting temperature, humidity, and other environmental conditions that could impact results. Regular performance validation helps optimize maintenance schedules and confirm that your filtration system maintains required efficiency levels.
Maintenance Requirements Assessment
Building on established performance metrics, proper maintenance requirements directly impact the longevity and effectiveness of dust removal systems. You’ll need to implement extensive maintenance protocols to guarantee peak filtration performance and system reliability.
- Monitor filter differential pressure readings daily and replace filters when they exceed manufacturer-specified thresholds
- Conduct regular system inspections of ductwork, seals, and collection units every 30 operating hours to identify potential leaks or damage
- Follow filter replacement schedules based on your specific cutting materials and operation intensity – typically every 2,000-3,000 hours for primary filters
- Document all maintenance activities, including pressure readings, inspection results, and component replacements for trend analysis
These maintenance requirements guarantee your dust removal system maintains specified collection efficiency while preventing unexpected downtime and extending equipment life. Proper upkeep also helps maintain workplace air quality standards and system performance specifications.
Energy Optimization Strategies
Operating a laser cutting dust removal system at peak efficiency requires implementing several key energy optimization strategies. You’ll need to focus on energy recovery systems and efficiency improvements to reduce operational costs while maintaining peak performance.
Strategy | Implementation |
---|---|
VFD Control | Install variable frequency drives on motors |
Heat Exchange | Implement air-to-air heat recovery systems |
Smart Scheduling | Program operation times based on usage |
Pressure Balance | Optimize static pressure in ductwork |
You can achieve significant energy savings by implementing advanced control algorithms that adjust fan speeds based on real-time particulate levels. Install pressure sensors throughout the system to monitor and automatically maintain peak airflow rates. Consider retrofitting your existing system with high-efficiency motors and smart controllers that enable precise power management. Additionally, you’ll want to incorporate heat recovery modules that capture and reuse thermal energy from exhaust air, particularly during winter months when heating costs are higher.
Monitoring and Control Systems
To maintain ideal performance of your dust removal system, a detailed monitoring and control network must integrate multiple sensor types and automated response mechanisms. System integration guarantees seamless communication between components while real-time monitoring enables immediate responses to changing conditions.
Your control system should incorporate these critical elements:
- Particulate matter sensors that continuously measure dust concentrations at key collection points
- Differential pressure monitors across filter elements to detect potential blockages or failures
- Flow rate sensors that verify proper air velocity through ducting networks
- Smart controllers with automated threshold responses and system diagnostics
When you implement extensive monitoring, you’ll receive instant alerts about system anomalies, allowing for rapid intervention before issues escalate. Modern control interfaces provide detailed performance metrics, maintenance schedules, and predictive analytics. By leveraging these advanced monitoring capabilities, you’ll optimize filtration efficiency while reducing operational costs through preventive maintenance and automated adjustments.
Maintenance Requirements and Best Practices
While sophisticated dust removal systems are engineered for reliability, they require systematic maintenance protocols to sustain peak performance and extend operational life. You’ll need to implement regular preventive maintenance schedules and conduct routine inspections to guarantee ideal functionality.
Maintenance Task | Frequency | Action Required | Impact |
---|---|---|---|
Filter Changes | Monthly | Replace filters | Airflow optimization |
Duct Inspection | Quarterly | Clean/repair ducts | System efficiency |
Motor Assessment | Bi-annual | Performance check | Downtime reduction |
System Calibration | Annual | Full evaluation | Peak performance |
To maintain cleanliness standards, you should establish service contracts with qualified technicians. Performance evaluation metrics help identify when system upgrades are necessary. Equipment replacement schedules must align with manufacturer specifications and usage patterns. Best practices include maintaining detailed maintenance logs, scheduling servicing during off-peak hours, and implementing automated monitoring systems. This proactive approach minimizes unexpected breakdowns and guarantees consistent dust removal efficiency.
Environmental Impact and Regulatory Compliance
Since dust removal systems directly impact environmental quality, compliance with regulatory standards is crucial for responsible operation. You’ll need to conduct regular environmental assessments and guarantee your system meets current emissions standards across multiple regulatory frameworks. Implementing sustainable practices helps minimize your facility’s environmental footprint while maintaining operational efficiency.
- Monitor particulate matter concentrations to comply with local air quality regulations and maintain levels below prescribed thresholds
- Document all filtration system performance metrics and maintain records for regulatory inspections
- Implement proper disposal protocols for collected particulates according to hazardous waste management guidelines
- Install continuous emissions monitoring systems (CEMS) to track real-time environmental impact
Your system must adapt to evolving environmental regulations while maintaining peak performance. Consider upgrading components to meet stricter emissions requirements and incorporating energy-efficient technologies that reduce overall environmental impact. Regular consultation with environmental compliance experts guarantees your system remains within acceptable operational parameters.
Cost Analysis and Return on Investment
When evaluating dust removal and smoke exhaust systems for laser cutting machines, a thorough cost-benefit analysis becomes essential for informed decision-making. You’ll need to take into account initial equipment costs, installation expenses, and ongoing operational requirements to develop an effective investment strategy.
Your cost analysis should factor in energy consumption, filter replacement intervals, maintenance schedules, and system downtime impact. Calculate potential savings from improved air quality, reduced equipment wear, and enhanced worker productivity. Modern dust removal systems typically deliver ROI within 12-24 months through decreased maintenance costs and extended machine life.
You’ll also benefit from analyzing long-term value factors such as compliance cost avoidance, reduced liability risks, and lower insurance premiums. Take into account scalability options and future expansion capabilities when determining your investment approach. Energy-efficient systems might qualify for environmental incentives or tax benefits, further improving your ROI metrics.
Conclusion
You’ll find that implementing an optimized dust removal and smoke exhaust system delivers measurable benefits for your laser cutting operations. With proper system design achieving 99.97% filtration efficiency through HEPA media, you’re ensuring both worker safety and equipment longevity. By integrating VFD-controlled motors and real-time monitoring systems, you’ll reduce energy consumption by up to 30% while maintaining consistent extraction performance across varying production loads.