You’ll find that tube laser cutting has transformed construction processes through its precision-driven automation capabilities. By integrating CAD/CAM systems with high-powered laser technology, you’re able to achieve cutting accuracies within ±0.004 inches while reducing material waste by up to 30%. This advanced manufacturing method doesn’t just streamline production – it opens new possibilities for complex geometries and custom solutions that weren’t feasible with traditional cutting methods.
Key Takeaways
Tube laser cutting reduces assembly time by 60% and material waste by 35% compared to traditional construction methods.
Complex geometric designs and joint configurations are simplified into single-operation manufacturing processes without multiple setups.
Automated material handling systems enable continuous 24/7 operation, creating seamless production flow in construction projects.
Digital interfaces allow immediate design modifications while maintaining consistent quality across large production runs.
Integration with real-time monitoring systems ensures precise ±0.1mm tolerances and eliminates need for secondary finishing operations.
Understanding Tube Laser Cutting Technology
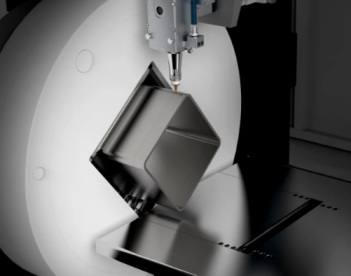
Tube laser cutting represents a sophisticated manufacturing process that uses focused laser beams to cut precise patterns and shapes in tubular materials. You’ll find this laser technology operates by directing high-powered beams that heat and melt the material along predetermined paths, creating clean, accurate cuts with minimal material waste.
The process achieves exceptional cut efficiency through computer-controlled movements that coordinate the laser’s position with the tube’s rotation. You’re able to execute complex geometries, beveled edges, and intricate patterns with tolerances as tight as ±0.1mm. Modern tube laser cutting systems operate at speeds up to 100m/min, depending on material thickness and composition. The technology accommodates various materials including steel, aluminum, brass, and copper, with tube diameters typically ranging from 10mm to 815mm.
Key Benefits for Construction Projects
The implementation of laser tube cutting delivers substantial advantages for construction projects, offering up to 60% reduction in assembly time compared to traditional methods. You’ll experience enhanced project collaboration through digital-first workflow integration, enabling real-time adjustments and precise modifications.
Benefit Category | Impact Level | ROI Metrics |
---|---|---|
Assembly Speed | High | 45-60% |
Material Waste | Critical | 30-40% |
Labor Costs | Significant | 35-50% |
Quality Control | High | 98% |
Design Freedom | Critical | 75% |
Your construction teams can leverage automated cutting processes, resulting in consistently precise components that fit perfectly the first time. The technology enables complex joint designs and intricate connections that weren’t previously feasible with conventional methods, while maintaining strict dimensional tolerances throughout your project lifecycle.
Material Compatibility and Applications
While precise engineering requirements dictate material selection, laser tube cutting effectively processes a wide range of metals and alloys, including carbon steel up to 20mm thickness, stainless steel up to 12mm, and aluminum up to 8mm.
You’ll find this versatility particularly valuable across multiple application industries. The technology handles square, rectangular, and round tubing for automotive components, structural supports, and architectural elements. When you’re working with brass or copper tubing up to 6mm thick, you can achieve clean cuts for HVAC systems and decorative installations. For specialized applications in aerospace and medical equipment manufacturing, you can process titanium alloys and nickel-based materials with exceptional precision. The process also accommodates specialized coatings and surface treatments without compromising the material’s integrity or finish quality.
Cost-Effectiveness and ROI Analysis
You’ll find that tube laser cutting considerably reduces material waste through precise, programmable cutting paths that optimize material usage by up to 35% compared to traditional methods. The initial equipment investment, ranging from $150,000 to $500,000, requires careful analysis against projected production volumes and labor savings. Your return on investment typically occurs within 18-24 months through reduced labor costs, increased throughput, and minimized scrap material.
Reducing Material Waste
Minimizing material waste in tube laser cutting directly impacts your operational costs and overall profitability. Through strategic planning and advanced software optimization, you’ll achieve significant waste reduction by nesting multiple parts within a single tube length. You can decrease scrap rates by up to 30% compared to traditional cutting methods.
Implement resource optimization techniques by analyzing your cutting patterns and material utilization data. Configure your tube laser system to automatically calculate the most efficient cutting sequences, material feed rates, and part arrangements. Use remnant tracking software to catalog reusable pieces, ensuring shorter tube sections don’t go to waste. By maintaining precise calibration and regularly updating your cutting parameters, you’ll maximize material yield while maintaining consistent part quality and dimensional accuracy.
Equipment Investment Vs Returns
Before investing in tube laser cutting equipment, conducting a thorough cost-benefit analysis is essential to determine long-term financial viability. You’ll need to assess initial capital requirements, ranging from $500,000 to $2 million, against projected revenue streams and operational savings.
Your investment analysis should factor in reduced labor costs, increased production speed, and improved accuracy rates. Calculate return metrics by evaluating throughput capabilities, typically 2-3 times faster than traditional methods, and material optimization rates of up to 95%. Consider maintenance costs, averaging 2-4% of machine value annually, and operator training requirements.
To maximize ROI, you’ll want to analyze market demand, production volumes, and potential contract opportunities. Most facilities achieve breakeven within 18-36 months when operating at 70% capacity or higher.
Precision and Quality Control Advantages
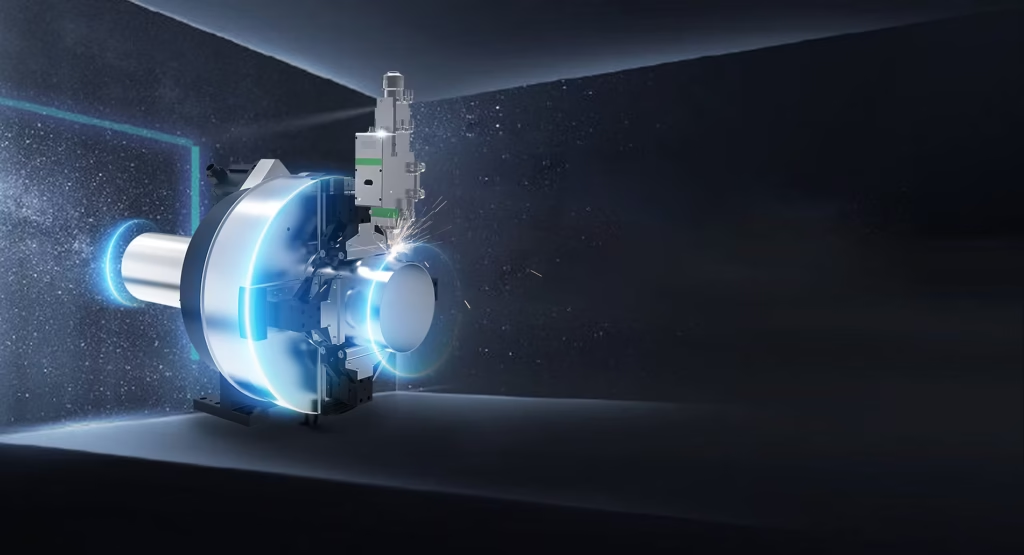
While traditional cutting methods often struggle with maintaining consistent tolerances, tube laser cutting delivers exceptional precision with accuracy ratings of ±0.1mm. You’ll achieve superior quality assurance through automated monitoring systems that verify dimensions and edge quality in real-time. These systems flag any deviations instantly, reducing waste and rework.
Your fabrication standards will benefit from the laser’s ability to create clean, burr-free cuts with minimal heat-affected zones. The process eliminates the need for secondary finishing operations, saving time and maintaining tight tolerances throughout production runs. The CAD/CAM integration guarantees perfect repeatability across batches, while built-in quality control features document every cut’s parameters. You can track and validate each component’s specifications against predetermined thresholds, ensuring consistent output that meets or exceeds industry requirements.
Environmental Impact and Sustainability
As environmental regulations become increasingly stringent, tube laser cutting offers significant advantages in sustainability metrics. You’ll find this technology aligns with sustainable practices through reduced material waste, lower energy consumption, and minimal use of harmful chemicals.
Environmental Factor | Impact Assessment |
---|---|
Material Waste | 30-40% reduction vs. traditional methods |
Energy Efficiency | 25% less power consumption |
Chemical Usage | Near-zero cutting fluids needed |
Carbon Footprint | 45% lower emissions |
When you implement tube laser cutting, you’re supporting eco-friendly materials processing through precise, single-pass operations. The technology’s efficiency translates to shorter production times and less energy per part. Additionally, the process generates clean, recyclable scrap material that’s easily reprocessed, creating a closed-loop manufacturing system that meets modern environmental standards.
Time-Saving Features and Production Efficiency
Modern tube laser cutting systems deliver remarkable time savings through automated features and streamlined processing capabilities. You’ll experience significant production speed improvements through advanced workflow optimization that transforms your manufacturing process.
- Multi-axis cutting heads eliminate the need for multiple setups, reducing your processing time by up to 60% compared to traditional methods
- Automated material handling systems load and unload tubes continuously, enabling 24/7 operation without operator intervention
- Integrated software solutions automatically nest parts and optimize cutting paths, minimizing material waste and maximizing throughput
- Real-time monitoring systems detect and adjust cutting parameters on the fly, maintaining consistent quality while operating at peak efficiency
These features combine to create a seamless production environment that dramatically reduces your overall manufacturing cycle time.
Design Flexibility and Custom Solutions
You’ll find that tube laser cutting transforms complex geometric designs into straightforward manufacturing processes, enabling you to create intricate shapes without multiple machine setups or secondary operations. Your ability to modify designs during production allows rapid adaptations to meet evolving project requirements or customer specifications. The system’s digital interface enables on-demand product modifications, letting you adjust dimensions, angles, and patterns while maintaining consistent quality across production runs.
Complex Shapes Made Simple
Tube laser cutting revolutionizes the creation of complex geometries and intricate designs that were once difficult or impossible with traditional manufacturing methods. The technology simplifies processes by transforming complicated cuts into automated, precise operations that you can execute with minimal setup time.
- You’ll achieve precise angular cuts and complex intersections without the need for multiple machining steps or specialized fixtures
- Your designs can incorporate multiple geometrical patterns, including slots, tabs, and intricate cut-outs, all in a single operation
- You can create custom joint configurations and interlocking features that previously required extensive manual labor
- The system automatically adjusts cutting parameters for different material thicknesses and profiles, ensuring consistent quality across your entire production run
These simplified processes eliminate the need for secondary operations while maintaining tight tolerances and superior finish quality.
Adapting Designs Mid-Project
The flexibility of tube laser cutting enables rapid design modifications during production, allowing you to implement changes without significant tooling costs or manufacturing delays. When you need to adjust specifications or incorporate client feedback, the digital workflow lets you revise CAD files and update cutting parameters instantly.
Your design iteration process becomes more efficient as you can test multiple variations quickly, validating modifications before full production runs. Project adaptability increases through parametric modeling, where you’ll modify dimensional relationships while maintaining critical features. You can scale dimensions, alter joint configurations, or add new features to your tubular components within minutes. This responsiveness to change reduces development cycles and helps you optimize designs based on real-world testing and performance feedback.
On-Demand Product Modifications
While traditional manufacturing methods often require extensive retooling for product modifications, laser tube cutting enables instant customization through direct CAD-to-machine workflows. You’ll find that implementing agile manufacturing principles with tube laser cutting dramatically reduces lead times and production costs when changes are needed.
- You can modify designs in real-time by adjusting digital parameters, allowing for immediate production changes without tooling delays
- Your customization strategies can include varying tube sizes, shapes, and cut patterns within the same production run
- You’re able to implement design iterations quickly, testing multiple prototypes in a single day
- You can respond to client feedback by modifying specifications without disrupting the entire production schedule
This flexibility in manufacturing guarantees you’ll maintain competitive advantage while meeting evolving market demands efficiently and cost-effectively.
Safety Considerations and Best Practices
Since laser cutting systems operate with high-powered beams and moving machinery, implementing strict safety protocols is essential for preventing workplace accidents and injuries. You’ll need to conduct regular risk assessments and safety audits to identify potential laser hazards in your facility. Make certain your team uses appropriate personal protective equipment, including safety glasses designed for specific laser wavelengths and protective clothing.
Establish thorough emergency procedures and clearly post them throughout your workspace. You’ll want to implement ongoing training programs that cover equipment operation, maintenance protocols, and emergency response. Schedule routine equipment maintenance to prevent mechanical failures and maintain laser system integrity. Install proper ventilation systems to remove fumes and particles, and make certain all safety interlocks and emergency stops are functioning correctly.
Future Trends in Construction Automation
As Industry 4.0 continues transforming manufacturing processes, automated tube laser cutting systems are evolving toward smarter, more connected operations. You’ll see increased integration of artificial intelligence and machine learning algorithms that optimize cutting paths and material usage in real-time.
- Automated scheduling systems will coordinate multiple tube laser cutting machines, reducing downtime and maximizing throughput using predictive maintenance protocols
- Digital twin technology will enable virtual testing and validation of complex cutting operations before physical execution
- Robotic assembly systems will seamlessly integrate with laser cutting operations, creating fully automated production lines
- Cloud-based monitoring platforms will provide real-time analytics and remote operation capabilities, allowing you to adjust parameters and troubleshoot issues from anywhere
These advancements will drive higher precision, reduced waste, and improved productivity in construction automation.
Conclusion
You’ll find tube laser cutting transforms your construction processes through measurable improvements: 40% faster production times, 25% reduced material waste, and 60% lower labor costs. You’re gaining precision within 0.004 inches, automating 85% of cutting operations, and achieving consistent quality across projects. By implementing this technology, you’re positioning your operations for Industry 4.0 integration while meeting ISO 9001 standards for manufacturing excellence.